Taking offshore even deeper with X80 grades for risers and flowlines
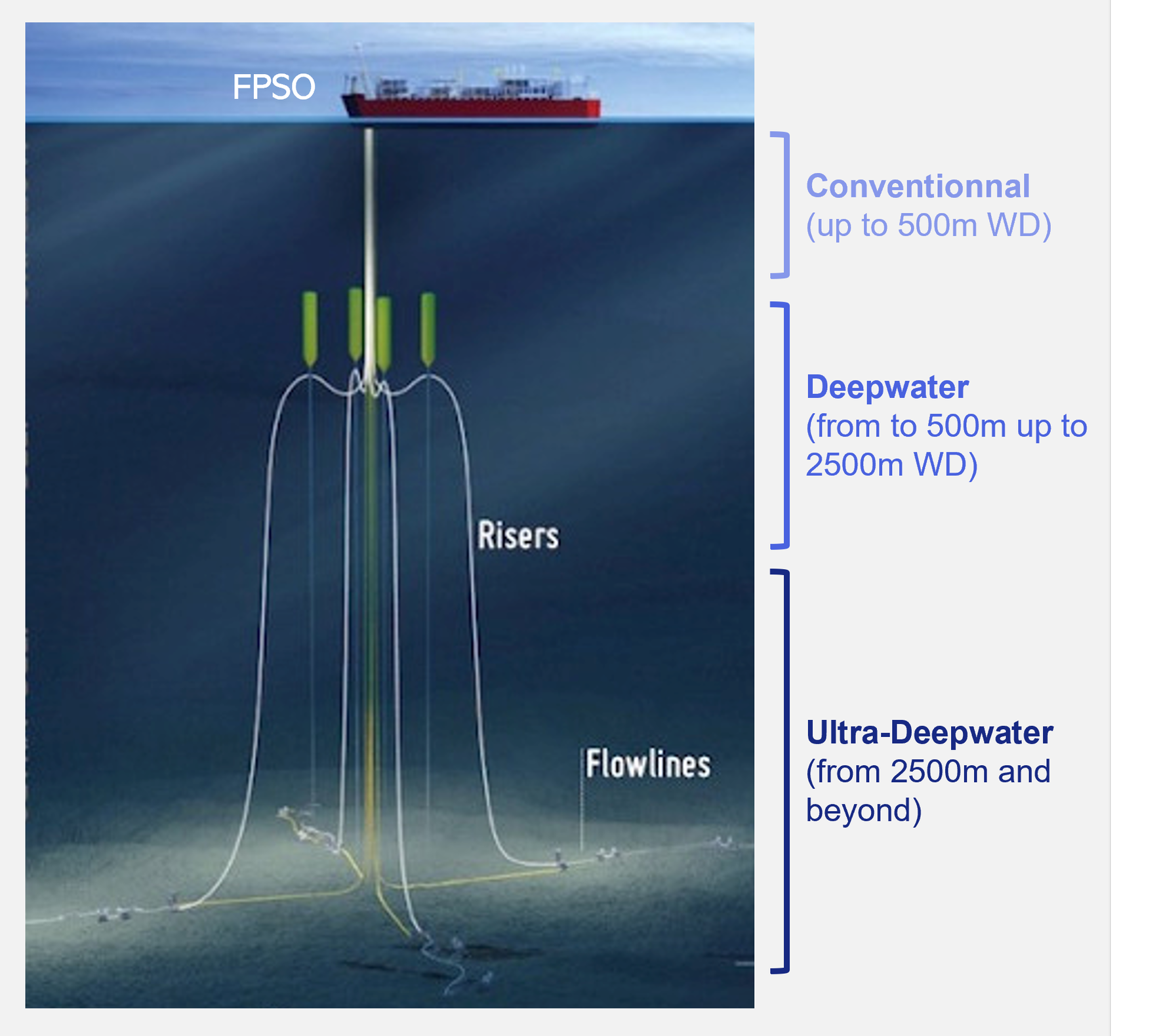
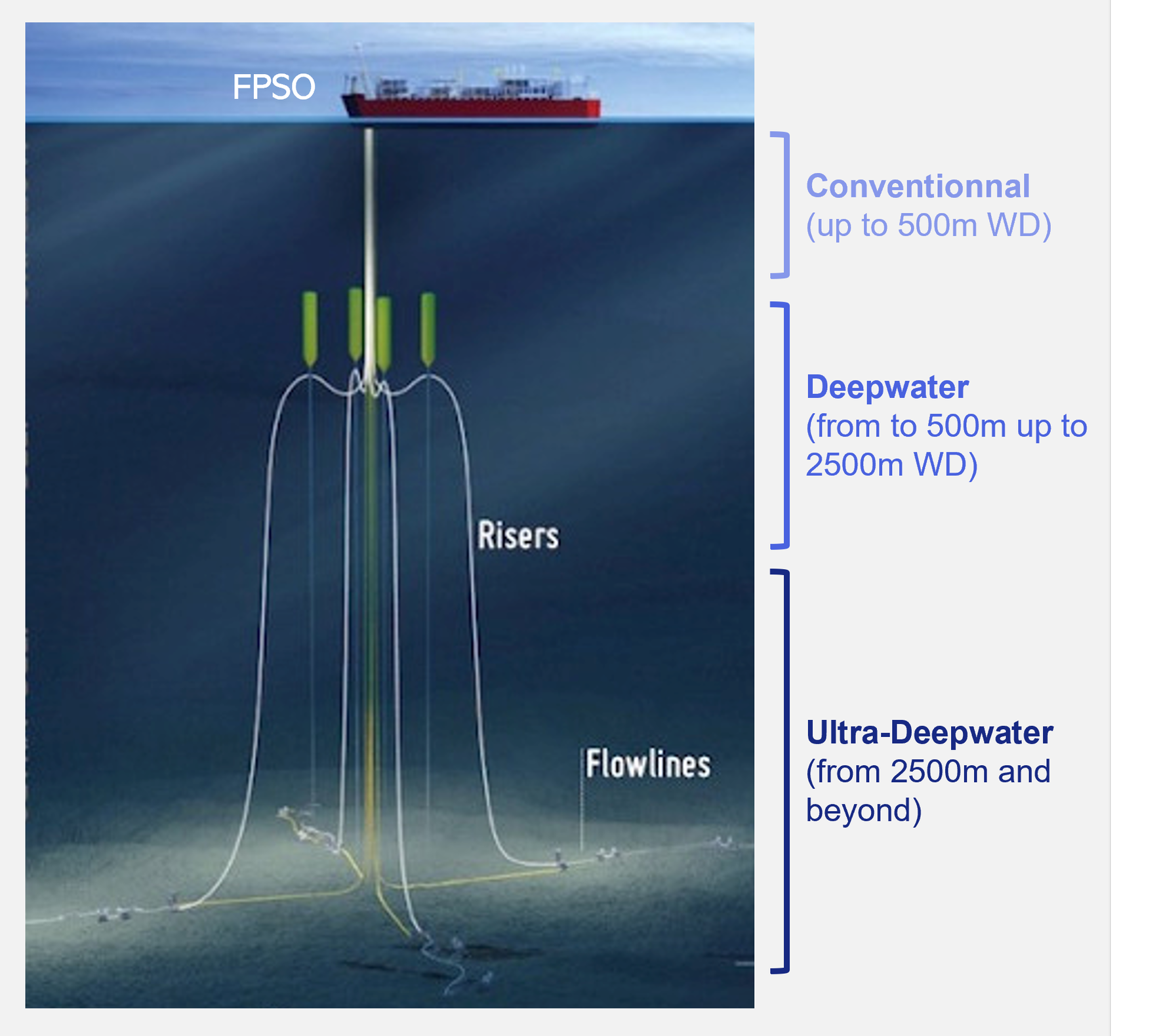
Last April, Vallourec held a live webcast in conjunction with the Pipeline & Gas Journal, exploring solutions for ultra-deepwater applications. Harold Evin, Vallourec’s Marketing, Research & Development Director for Project Line Pipe, presented details about the X80 steel grade. He explained the pipe and weld qualification process and X80’s role in enabling operators to build even deeper offshore wells.
Ultra-deepwater offshore projects, defined as those of 1,500 meters and deeper, create very specific engineering challenges. Extreme depths result in high hydrostatic pressure which can lead to collapse issues or buckling during installation phases. In addition, longer risers with increased load will experience fatigue during their lifetime. Lastly, ultra-deep field development, with its complex layouts and installations, calls for more accessories, such as buoyancy modules, which generate higher project costs.
To rise to the challenges of demanding line pipe projects, Vallourec has developed a comprehensive pipe grade portfolio, which includes the X80 steel grade.
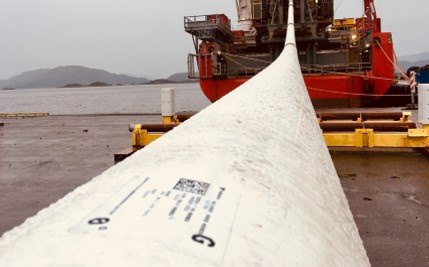
A robust tool for stringent environments
By meeting the material challenges for operational welding, Vallourec’s X80 steel grade offers both sour service and fatigue sour service resistance. The benefits of risers made of X80 grade include:
- Reduced wall thickness compared to standard X65 line pipe grades for similar design pressures
- Less weight, reducing the need for buoyancy modules
- Less steel manufactured per project, meaning reduced CO2 emissions
- Greater flexibility for pipelaying by the installation vessel
Vallourec’s first seamless X80 grade has now been delivered for pipes with heavy wall thickness up to 40mm and for mild sour applications (NACE region 2). For such applications, X80 guarantees a maximum hardness below 280 HV10 on the pipe, and an average toughness of 300J at -30°C. Vallourec has been developing the X80 solution over the last 10 years, working with various engineering, procurement, and construction (EPC) partners who attest to its impressive performance in mild sour environments.
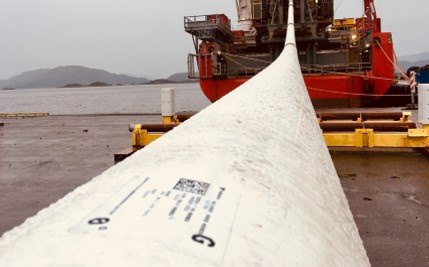
Rigorous testing for new applications
For example, Vallourec—together with Subsea 7 and ExxonMobil—have performed small-scale sour service fatigue tests of pipes and welds. These results, published at the 2022 AMPP Conference, have highlighted comparable corrosion fatigue performance for X80 welds and standard welds on X65.
Continuously innovating to push the boundaries of material grades, Vallourec is now working on the next X80 steel grade concept to address full sour service applications in NACE region 3. This solution is targeting wall thicknesses below 30 mm. Thanks to specific composition and manufacturing processes, lower hardness will be achieved for the pipe and subsequent welds. The first four point bend tests performed on this new concept, all following NACE TM0316 standards, are already showing good performance.
“Looking at these results, it is evident that X80 is a great material for challenging offshore deepwater projects in sour service environments”, Harold said.
X80 performs in the field
Harold presented a case study exploring how X80 improves riser designs and lowers installation costs.
“In the field, we found that using X80 instead of X65 reduced wall thickness by up to 20%. This resulted in weight savings on the riser which translated into time and costs savings during installation.”
Another example given was a project where a riser made of 41 mm thick pipes in X65 steel required the use of buoyancy modules in what is known as a steel lazy wave riser (SLWR) configuration. In this specific case, using X80 reduced wall thickness of the riser pipe to 32 mm, which in turn eliminated the need for buoyancy modules. By enabling a steel catenary riser configuration (SCR), X80 can lower project installation costs. Indeed, reducing wall thickness eliminated more than 2,000 tons of steel production, which translated to cost savings of around $2,800/ton. It also shortened installation time by a full 12 days and saved up to 3,500 metric tons of CO2 emissions.
Taking operators deeper and deeper
“The development of Vallourec’s X80 grade steel for offshore ultra-deepwater projects is the result of best-in-class manufacturing combined with extensive research and data collection,” Harold said. “It has also been made possible thanks to close collaboration with the world’s best EPCs.”
Vallourec’s X80 grades are now fully available, and operators are encouraged to contact Vallourec today to find out how these high-quality solutions can boost performance, save time and money, and shrink carbon footprint.
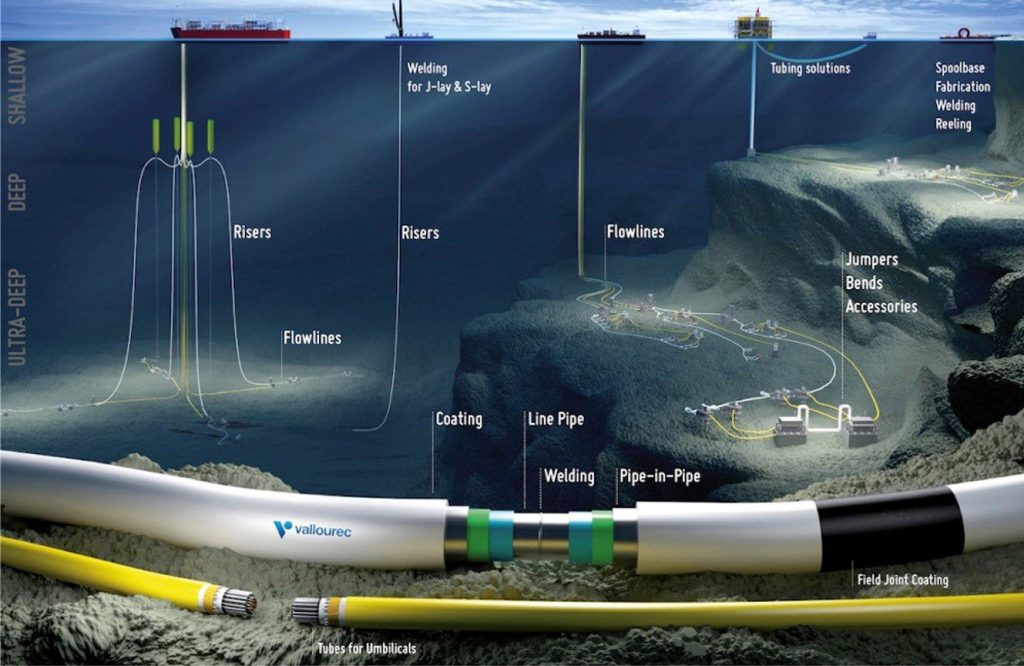