VAM® 21 Accessories: Validated for Different Material Assemblies
Every string in an oil and gas well is composed not only of pipes but also of various types of tubular accessories which are part of the well design, contribute to well integrity and facilitate operations. In most cases, these accessories are connected to the rest of the string by the same connection threaded onto the pipes. However, the steel material may vary, demanding in some cases specific validations. Vallourec has recently tested and validated the combination of different materials for accessory assemblies fitted with VAM®21 connections providing customers with safe and reliable production performance.
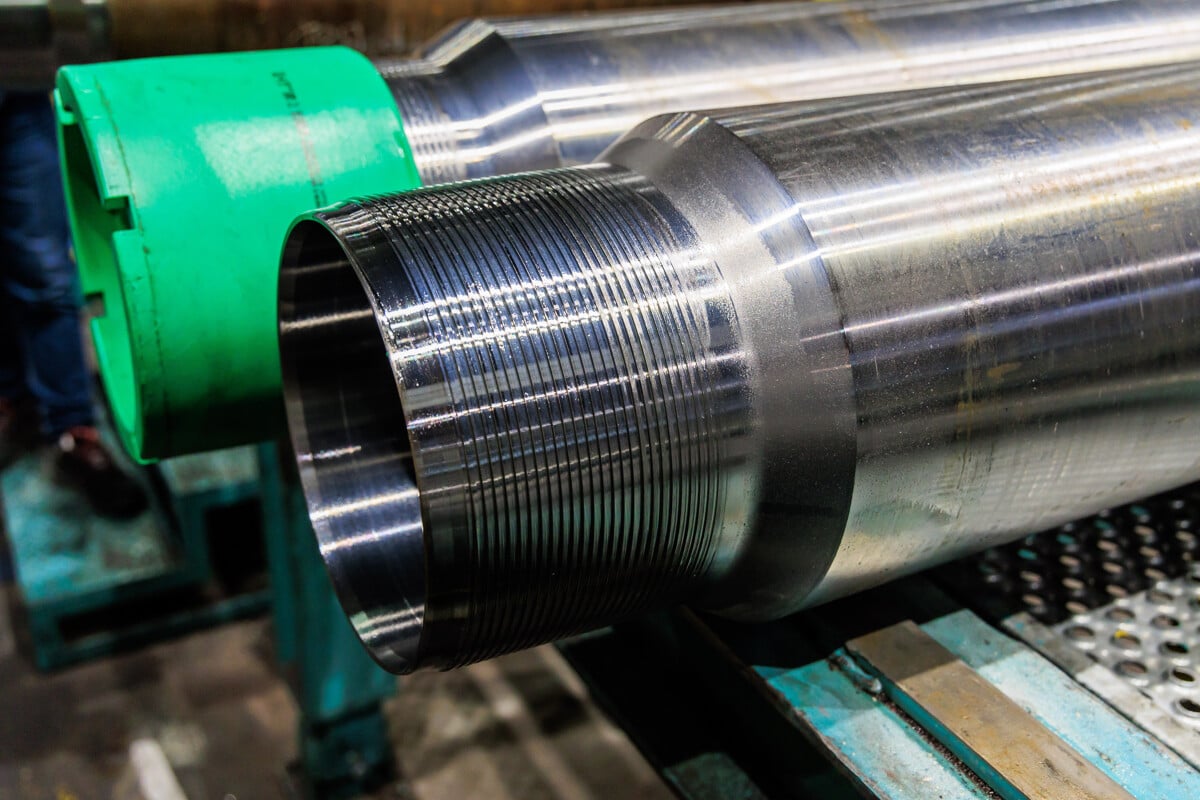
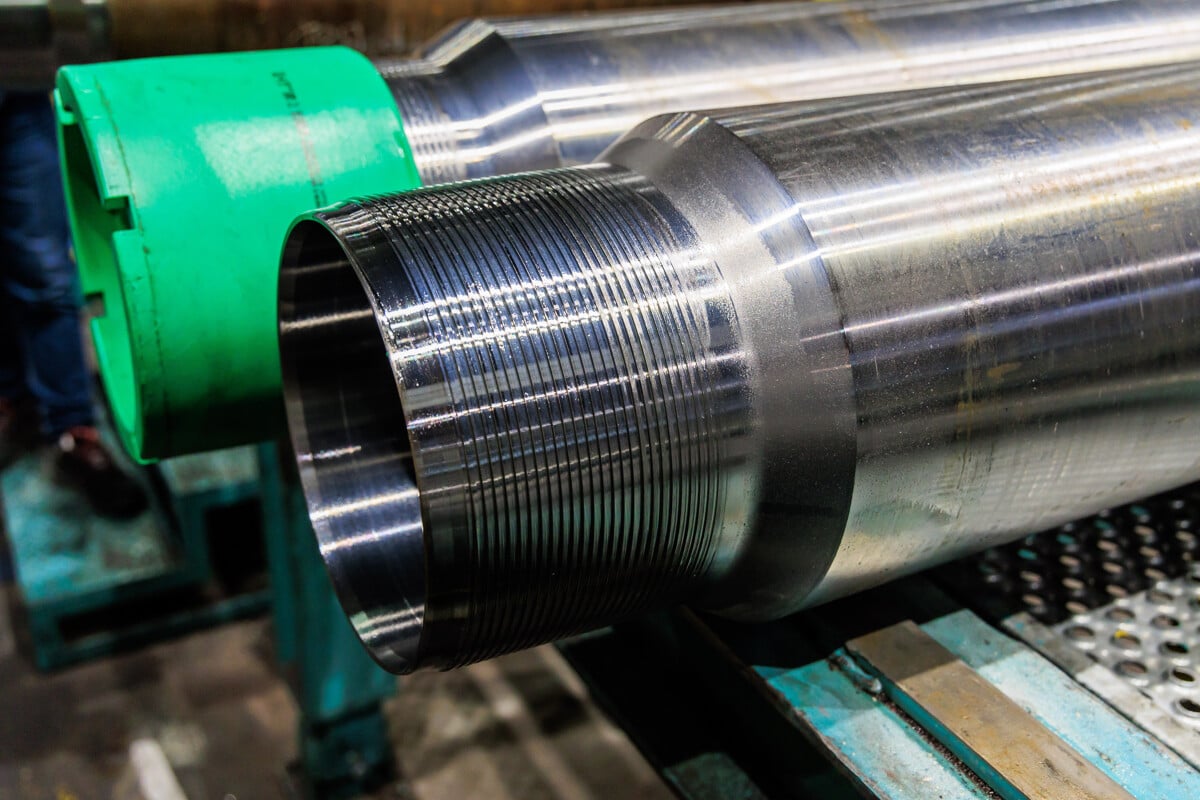
OCTG accessories are an important component of every well. Depending on the need, OCTG accessories connect casing and tubing in the well, assist in the running of pipes or customize the tubing string to optimize product efficiency.
In most cases, these accessories are connected to the pipes using the same connection as the one on the pipes, providing the same mechanical properties as the rest of the string. However, the material used to manufacture the accessories is most of the time different from the material used to manufacture the pipes, providing either a lower or higher Yield Strength or constituted of an altogether different steel grade. For example, casing hangers or completion accessories may be manufactured in Inconel and made up with sour service carbon steel casing. This material variation is due to the accessories’ different manufacturing process (forging) as well as to the use of proprietary grades which correspond to the equipment used by the OEMs.
In such cases, operators expect reliable support from the manufacturer, from the accessory design stage to its manufacturing, to ensure well integrity and smooth project execution as accessory manufacturing is often subjected to tight timeframe constraints. However, most industry manufacturers don’t provide accessory assembly test results, leaving an unknown variable.
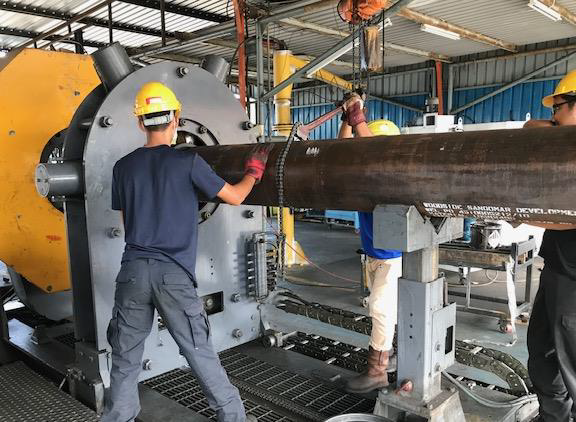
In order to provide operators with tangible proof of VAM® 21 accessories’ performance, whether for Oil & Gas drilling or for completion applications, VAM® Research and Development teams went beyond standard practices and carried out thorough technical evaluations and testing of the most common VAM® 21 interface threads found in well-heads, casing/liners and completion equipment. Among the interface threads evaluated and tested were some of the most demanding in the industry, including:
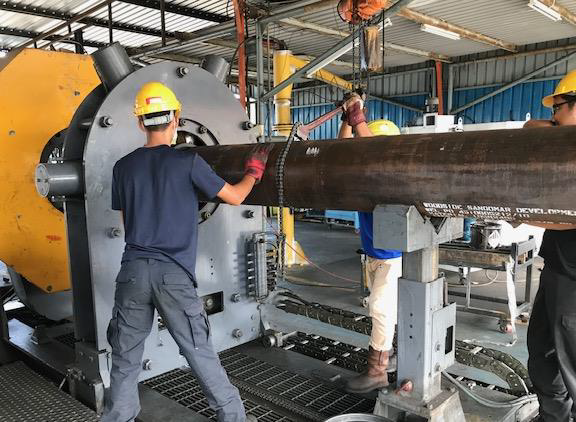
- Casing hanger manufactured in NACE compatible Low alloy steel (4130, F22) with 80 ksi MYS material made up with a 125 ksi MYS Carbon steel casing material. In this case, VAM® 21 needed to demonstrate its adaptability to a high YS mismatch between pin and box sides.
- High-strength casing hanger manufactured in Inconel 120 ksi MYS made up with a 110 or 125 ksi Sour Service Casing Hanger. In this case, VAM® 21 needed to demonstrate its capacity to be assembled properly even with galling-sensitive material such as Inconel 718
- VAM® 21 tubing hanger manufactured in Inconel inlay on low-alloy steel made-up with a 125ksi MYS tubing string in CRA material. In this case, VAM® 21 needed to demonstrate its adaptability to a galling-sensitive bi-material (Inconel 625 inlay on a F22 low-alloy steel).
- VAM® 21 threads integrated on completion equipment such as mandrels, subs, or crossovers, having grooves, transition angles, or ID/OD undercuts in close proximity to the VAM® 21 pin or box thread. In these cases, VAM® needed to demonstrate its capacity to integrate complex design shapes while maintaining equal thread performance levels.
All of the cases above were successfully assessed, tested and/or validated according to the latest internal Vallourec FEA standards as well as to international standards such as API 5C5-2017. Tests performed included, full-scale Make & Break, full-scale sealability testing and full-scale limit load tests.
The results confirmed VAM® 21’s high performance and robustness in the conditions listed above with a strong capacity to adapt to each specific case. The VAM® 21 design is therefore officially validated for interface threading for most of the Oil & Gas applications for which it is intended.
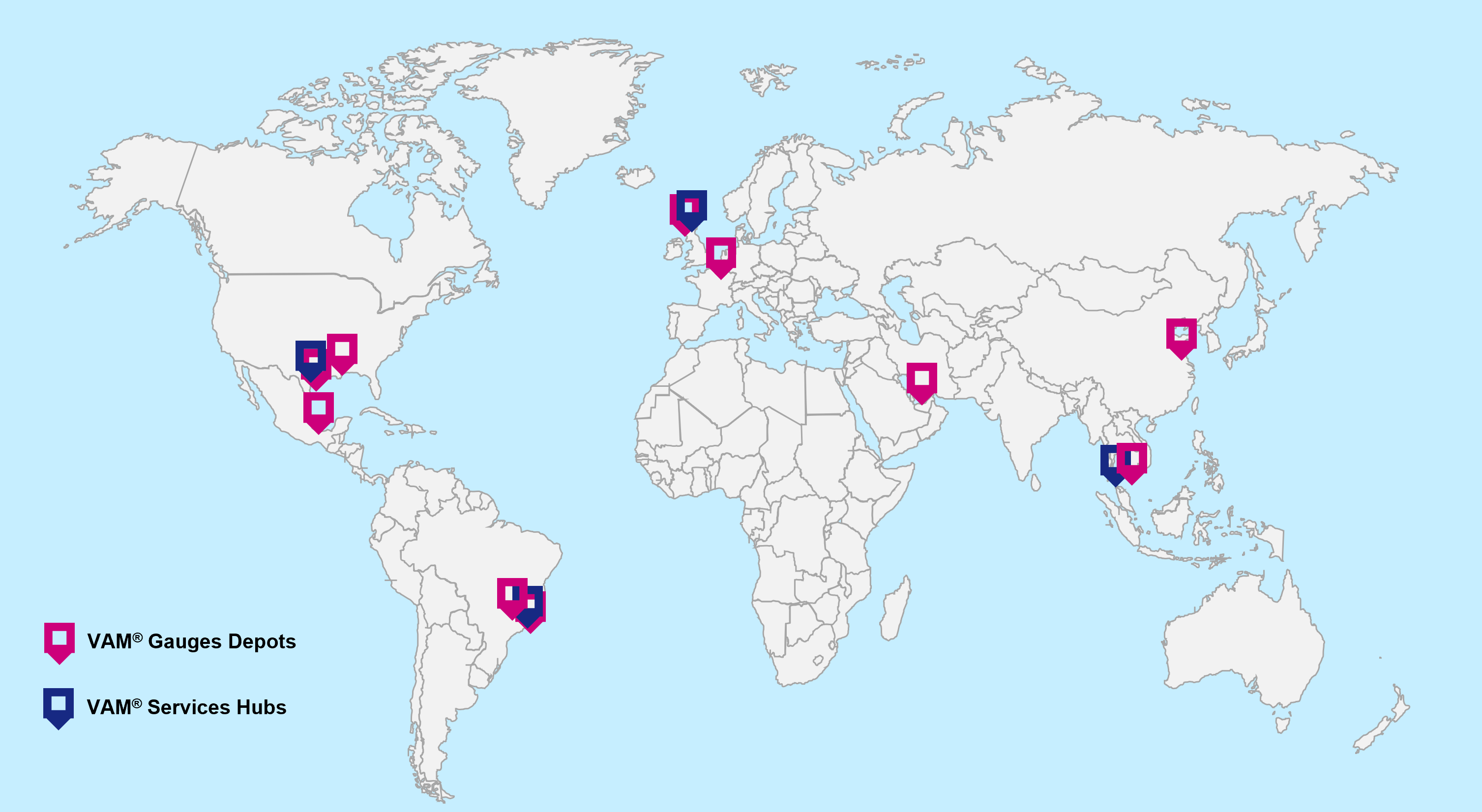
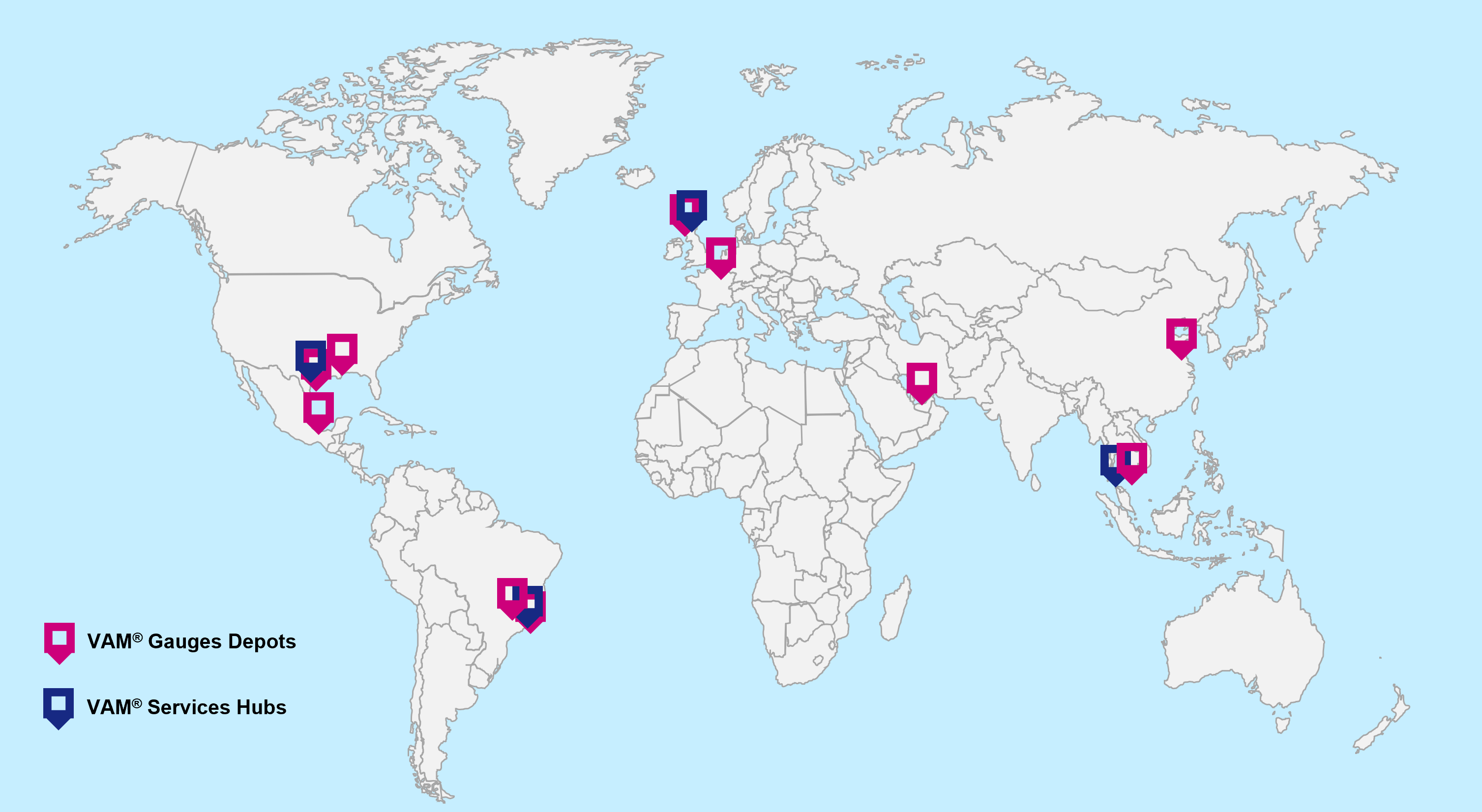
In addition to the reliability provided by these recent results, operators can count on receiving technical and manufacturing support from VAM® anywhere in the world.
Thanks to its extensive network of manufacturing centers, Vallourec is capable to thread VAM® 21 on any equipment in the main Oil & Gas hubs (USA, Mexico, Brazil, UK, France, Saudi Arabia, Dubai, Singapore, China). Vallourec is also supplying the major Oil Field Services companies thanks to its Unique Threading Cell concept, which provides a cost-effective solution with short lead times.
In addition, 137 VAM® Licensees located in 49 countries across the globe are currently qualified to manufacture VAM® connections–most of them qualified to manufacture VAM®21 connections. VAM® Licensees include local repair shops located close to customer operations which are able to provide a reactive service in terms of pipe repair or small accessories manufacturing such as pup joints or crossovers. Major OEMs such as Well Head Manufacturers or Completion Equipment Manufacturers who need to integrate VAM® connections within their own equipment design are also listed as VAM® Licensees.
Find the closest VAM® Licensee to your operations here
All VAM® Licensees are committed to manufacturing VAM® connections according to the same technical and quality standards. To ensure these standards are met, VAM® Services do regular audits and provide support and training to all Licensees. This includes:
- Online access to the technical documentation required to manufacture VAM® connections.
- Access to sets of calibrated gauges (over 9,000 sets) available thanks to 10 VAM® Gauge depots worldwide and several calibration centers. The gauges are usually supplied within a few hours of the request to maximum of 96 hours after.
- A technical evaluation performed at least on an annual basis consisting of an on-site audit performed by the VAM® Services auditor team.
- On-site product qualification
- A day-to-day technical support ensured by the VAM® Services auditor team and the VAM® Technical Support team. Mr. Help assistance processes in average 250 questions per month.
Best-in-class expertise
From designing and testing connections to providing on-site running assistance, VAM® prides itself in supplying its customers with safe and reliable solutions no matter their needs, anytime, anywhere. With the latest validation of accessory assemblies in different materials, VAM® covers an even wider range of customer needs, providing them with reassurance on their well’s integrity and performance.