A deep dive into the added value of VAM® Field Service
A deep dive into the added value of VAM® Field Service
14/06/2021 – VAM
Oil and gas operators have long reaped the benefits of using the VAM® Field Service (VFS) worldwide network of experts to ensure that VAM® best practices are deployed and operations run smoothly and efficiently. However, as VAM® Field Service Director Daniel Khoda Rahmi explains, by digging a little deeper, clients can get even more out of VFS than they realize.
VAM® Field Service includes more than 165 highly skilled technicians based in 17 service centers around the world. Their mission is to ensure that VAM® quality is maintained from mill to well by offering a range of services that cover the full lifecycle of customers’ pipes. VFS helps customers ensure operational performance by boosting rig operating efficiency and enables oil and gas operators to reduce costs.
Moreover, our VFS offer further comprises a wealth of string integrity management services, from pipe repair, to stock management, to quality and conformity inspections, as well as advisory services and rentals.
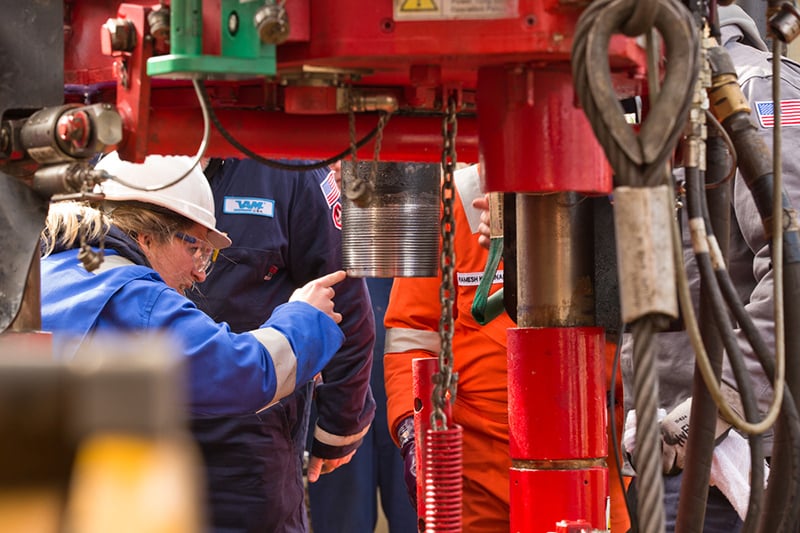
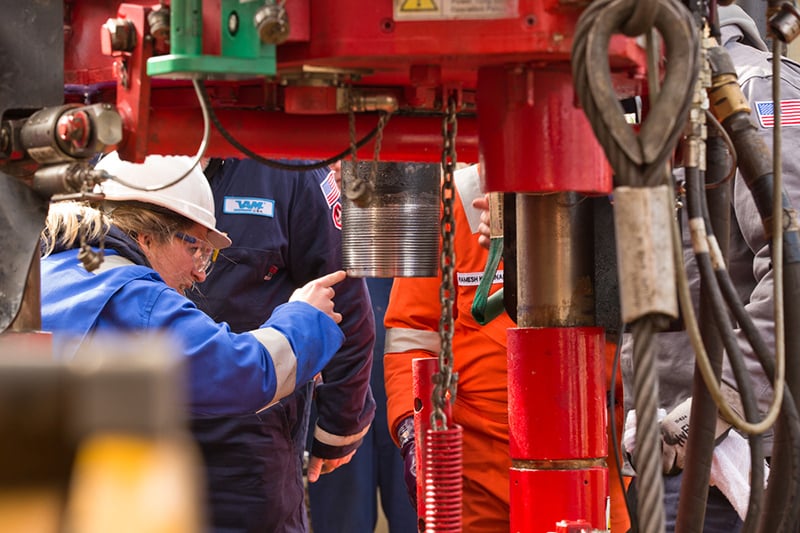
Key customer support that can save time, money – and lives
Beyond the usual verification and inspection service, VFS offers the key value-added service of troubleshooting. “A common misconception is that our technicians only review make-up graphs to determine whether or not they are acceptable,” says Daniel. “In reality, while technicians are onsite verifying pipes, they can also identify additional problems and directly propose safe and effective solutions.”
An example of this occurred recently when a VAM® technician on a client rig observed that the slip type elevator was not holding the pipe body; instead it was resting on the coupling face. “Our expert intervened immediately, halting operations and ordering new slips and dies to be helicoptered to the rig,” Daniel recalls. “Our expert’s swift decision-making not only prevented potential injury; it also saved the customer an estimated $1 million.”
VFS technicians can further manage activities throughout the installation process: supervising the process of pipe make-up, inspecting pipe stocking at yard, and providing quality and conformity checks.
Risk management for avoiding costly mistakes
The benefits of all these services cannot be under-estimated. Rig operators can enjoy greater operational efficiency, lower risk, and achieve 100% product integrity.
“I often compare pipe running to assembling flatpack furniture,” laughs Daniel. “When you are putting together new bookshelves, you can probably handle it yourself, but you can’t be 100% sure that you’re doing it right. It will take longer to build than if an expert did it, and you can’t guarantee the shelves are totally stable. The same is true for VFS – our customers can put pipes in place, but will they be aware of the best practices and parameters to get the most out of their connection?”
Despite the obvious benefits, some operators consider VFS an unnecessary additional insurance policy. However, seemingly benign statements like, “It’s only casing” and “We’ve always done it like this” have in the past resulted in catastrophic well integrity losses. The cost of such mistakes can be staggering. Operators can pay anywhere from $10 million in the event of a failed pressure test and re-run completion to $300 million for well shutdown and recompletion.
For Daniel, the cost of VFS is outweighed by savings in the case of an incident: “If the VFS technician repairs a damaged pipe, they can save operators a lot more in avoided pipe handling, repairs and downtime. Equally, if a mistake goes unnoticed in a make-up graph, an operator may need to pull out the full string, or deal with a leaking well. You can think of risk as the probability of a leak (low) multiplied by its potential consequences (very high). The outcome of that equation speaks for itself.”
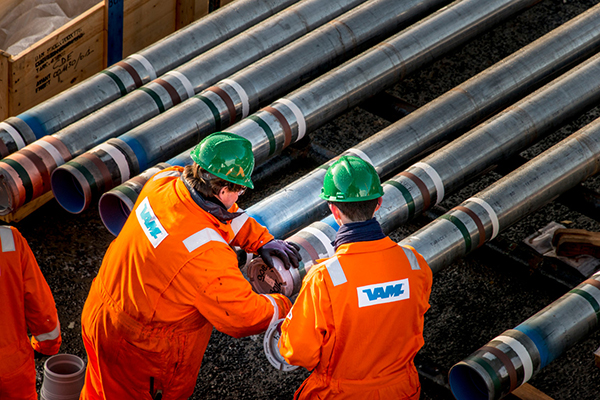
Innovating for the future
While the suite of services included in VFS offer is already large, we are constantly looking for ways to leverage digital technologies to improve our services. “We offer Realwear and HoloLens solutions for remote rig inspections. We can record these inspections and our customers are able to see in real time all relevant checkpoints right from their offices,” Daniel explains. “This is part of our existing and growing remote services offer for VFS, which is already adding value for customers while boosting safety and reducing costs.”
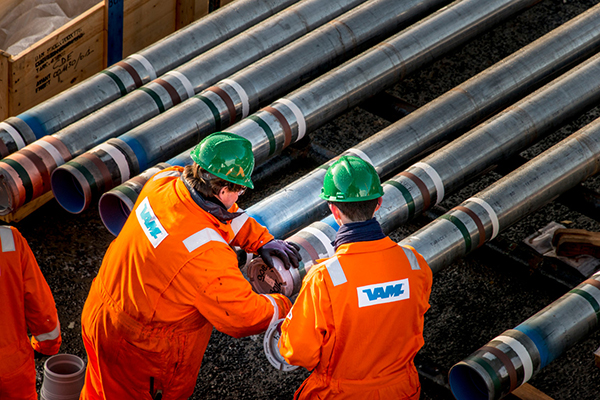
Vallourec is committed to enhancing irreplaceable in-person work with high value-added digital and remote services, providing clients with a comprehensive offer. “VFS technicians have supported oil and gas operators for decades,” Daniel concludes, “and we intend to ensure our offer develops in line with evolving industry needs moving forward. Remote services are the next big subject – and we already have operators buzzing about the work we’ve done so far.”
Stay tuned! Learn all about our remote VAM® Field Service (VFS) offering in our next article.