Behind the scenes with Vallourec R&D: Spotlight on Therma
Therma is Vallourec’s digital twinning tool that provides real-time piloting and monitoring of billet heating furnaces. Developed by ONE R&D in Aulnoye-Aymeries (formerly VRCF) in collaboration with colleagues around the world, Therma is now being deployed in numerous Vallourec sites.
The solution was created as part of Vallourec’s push to enhance our Industry 4.0 processes. In this article, ONE R&D Real-time Modelization Team Manager Guy Druart offers us an inside look at how Therma is being deployed, its advantages and evolution, and how Vallourec centers worldwide are making the most of this digital innovation.
Objective: one process model for greater productivity, less heterogeneity
Therma is a “twin” that uses advanced modeling to automatically pilot billet furnaces in the steel heating process that takes place before piercing and rolling. The last 30 years, and increasingly fluctuating workloads, have shown that controlling the process automatically, especially billet heating, ensures more efficient gas consumption and better-quality control.
Therma’s other massive innovation is that it can be used to simulate changes to furnace processes to predict their impact, thus eliminating much trial and error. The software’s “forecast of the future” algorithm allows for dynamic piloting of the furnace that takes into account production variability. “The result is more stable production with less thermal heterogeneity, and thus less pipe eccentricity,” Guy says. “Ultimately, this makes for a higher-quality product with reduced error and less temperature fluctuation.”
Environmental advantages
In the bigger picture, our planet will also benefit from this innovation. Furnaces piloted using Therma see an average increase in productivity of 15%, with a 5% reduction in gas consumption and CO2 emissions. An extra benefit of achieving a more stable product is a concurrent reduction in the number of scrap billets produced, or billets that engineers need to retreat and reheat – which involves a completely new furnace cycle. Less error means less waste of materials and fuel. “With gas prices so high right now, reduction in fuel usage offers us the ancillary benefit of cost savings,” Guy says.
Collaboration without borders
The huge Therma project is the result of a truly international collaboration. Within the Group, we’ve a solid “process community,” a big sponsor on this project, which allows us to easily reach out to far-off colleagues to initiate work. In this case, it began between IPE-A in Germany and the ONE R&D team in France using the Rath Pilger furnace as a pilot. After some initial success, the project’s processes and models were brought together on a single Shalyn platform with a unique web application so that even more teams could contribute. This got the Brazil VDIS (Vallourec Digital & Information Systems) team involved, after which even more participants such as plant engineers and thermal experts from around the world could be brought on board.
Today, further development of the tool continues and involves teams from France, Germany, Brazil, China, and the US. As they continue to work on optimizing the process model, the solution is already being implemented in our Jeceaba and Barreiro (Brazil) plants. And we’ll bring it to our plants in Tianda (China) and Youngstown (US) next. “A natural benefit is that once the tool goes live in one plant, all the other plants in our network will benefit from knowledge gained,” Guy adds.
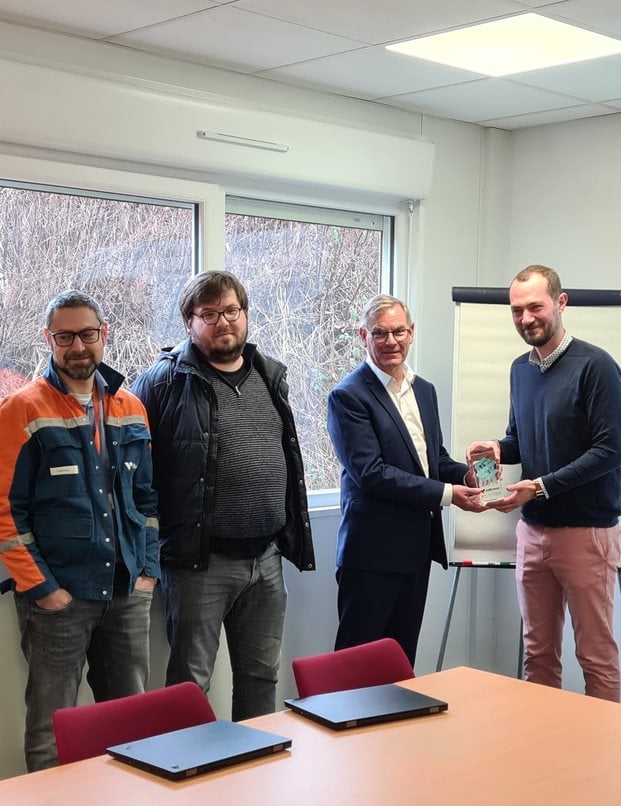
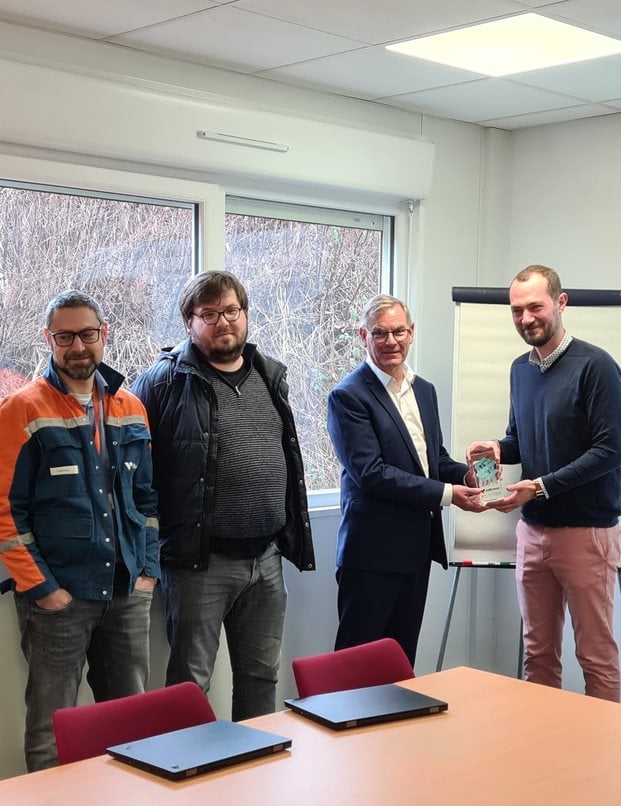
Philippe Guillemot is presenting the award to Marcello Bentivegni, Thomas Lenne and Guy Druart on behalf of the winning team, which also includes Ricardo Junqueira, Andre Gelbert, Glauco Oliveira and Helio Manetta.
Client focus plus environmental consciousness spells success
During the last R&D Day, organized internally, the Therma project won the Vallourec R&D Excellence Award in the Process category. It was chosen both for its innovation and worldwide scope, and for its environmental impacts. This award is a well-deserved celebration of the efforts and collaboration of a large number of people throughout Vallourec. Philippe Guillemot presented the award to the winning team during his visit to the Aulnoye-Aymeries site on January 31.
The benefits of deploying a digital twin for furnaces are myriad, and it is easy to see how those advantages could be extended to many other Vallourec processes. In fact, Vallourec will eventually use another model called Quench-R to obtain information about the cooling process: what is happening during the quench, and exactly how the billet is cooling.
While Therma focuses on heating and Quench-R will look at cooling, the equation powering the solution can be used to create further models. Data science models, for example can be used to forecast the mechanical properties of pipes. Achieving these models may not be easy, but the benefits of more stable production and access to the full “ID card” of a pipe cannot be overstated. Vallourec intends to continue developing these high value-added Industry 4.0 solutions as part of its commitment to serving clients and the industry better, every day.