CLEANWELL®: Setting New Standards for Wintershall Dea Projects in Norway
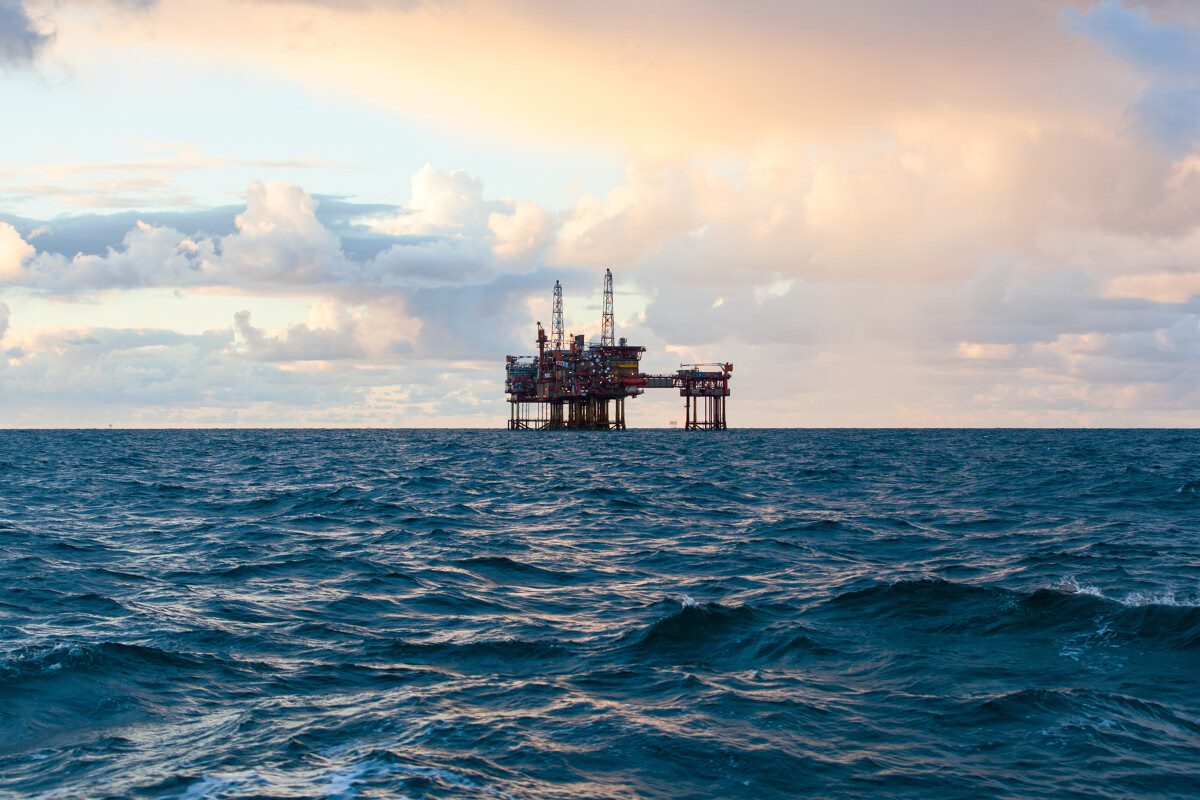
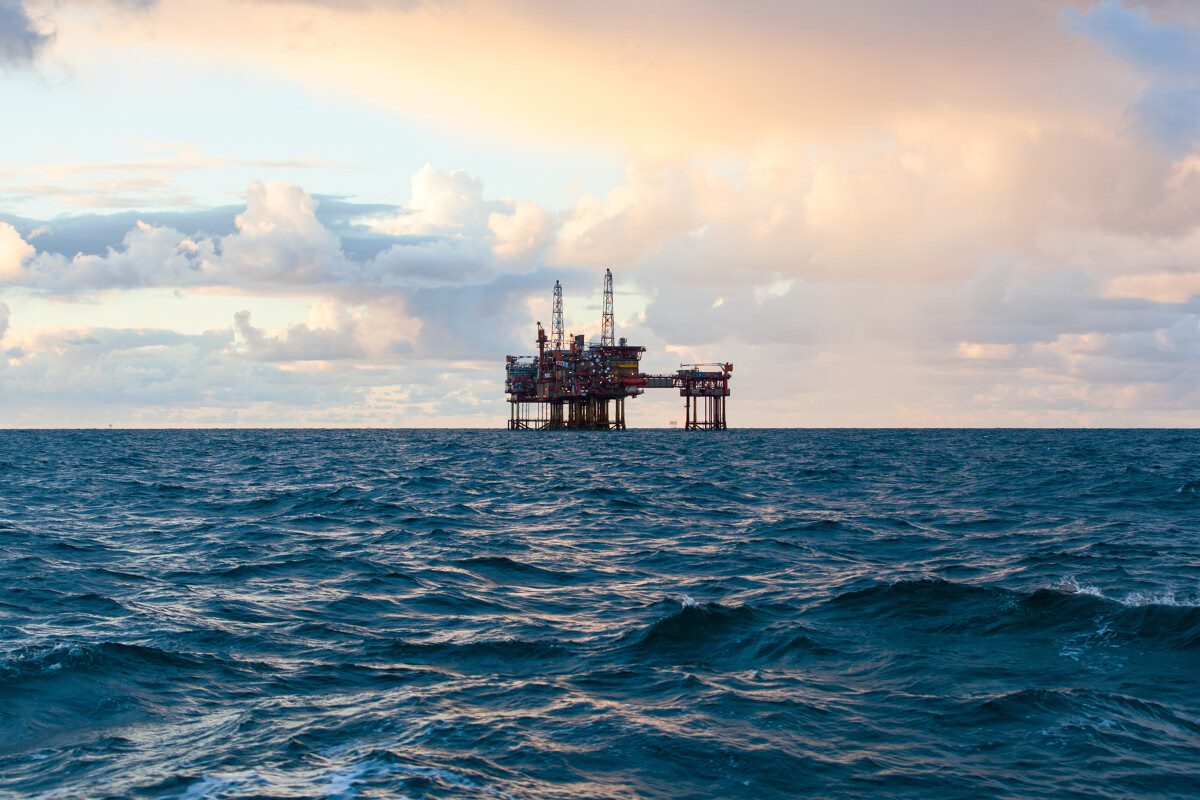
Committed to providing safety-conscious and environmentally-friendly solutions to its Oil & Gas operations, main operators on the Norwegian shelf are adopting dope-free solutions as part of their OCTG standards. CLEANWELL®, the VAM® dope-free solution, has been successfully used by Wintershall Dea on its recent projects, confirming the advantages and associated savings it provides throughout the OCTG product’s life cycle.
Stringent HSE-related regulations in Norway, such as REACH and OSPAR classifications, request Oil & Gas operators to eliminate all discharge to the environment. One of the contributors of discharge while running casing and tubing is running compound.
Motivated by this context and following an increasing trend towards dope-free solutions in the Norwegian shelf, Wintershall Dea approached Vallourec to work together on finding an environmentally-friendly alternative to thread compound without compromising performance. After some discussions, both companies came to the decision to try out Vallourec’s CLEANWELL® solution on Wintershall Dea operations.
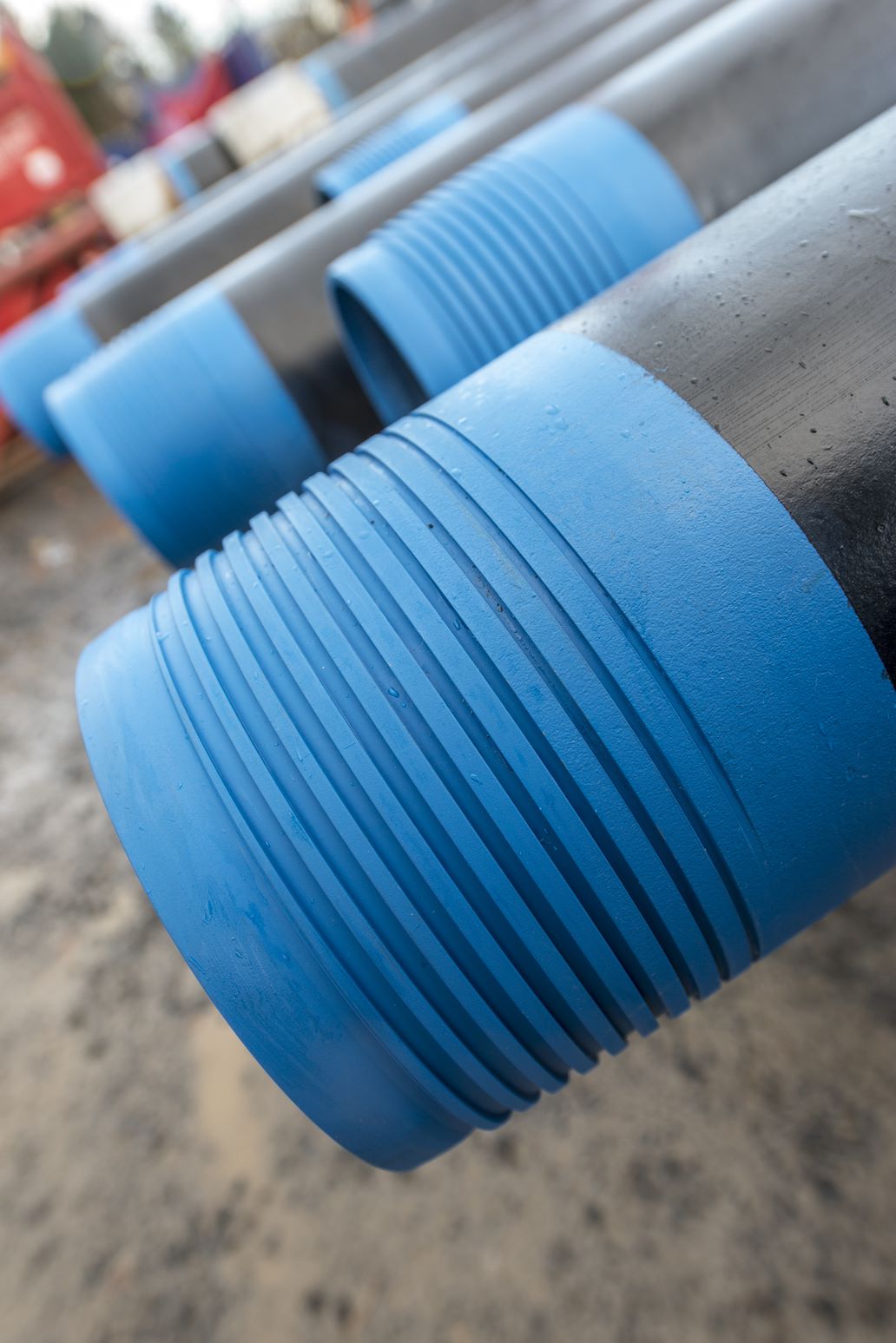
Developing a zero-waste solution
In the early 2000’s Vallourec started the development of its dope-free solutions to meet customers’ needs and environmental challenges. The latest and newest version is CLEANWELL®, a non-polluting, multi-functional coating which replaces both storage and running compounds and is applied directly on the surface of VAM® connections.
While there was no clear normative guidance on how to approach dope-free validation at the time, VAM® carefully assessed customer demands and developed a thorough validation methodology, ensuring that performances were compliant with the most stringent connection qualification norms. VAM® 21 CLEANWELL® has been the first product line extensively tested and validated based on this approach.
The validation included physical testing for sealability, torque and anti-galling behavior according to API RP 5C5:2017 / ISO 13679:2019 CAL-IV. In addition, the compatibility between a CLEANWELL® end with a regular doped end was assessed as per a similar stringent protocol, since this may be a common configuration when combining CLEANWELL® with standard dope pipes and accessories is required. The first full-length CLEANWELL® line was deployed at Vallourec’s mill in Aulnoye-Aymeries in France.
CLEANWELL® technology relies on two key features:
- A metal plating concept, ensuring anticorrosion and anti-galling performances. The robustness and durability of the plating has been assessed though accelerated cyclic corrosion tests and outdoor exposure in various climates proving storage resistance for over 3 years.
- A thermoset lubricant applied on top of the electro-plated surface completes the solution, providing extreme repeatability and stability throughout make-up, since it is carefully controlled at the mill (thus not subjected to the common variability observed upon dope usage, regarding its nature, application process, quantity and so on).
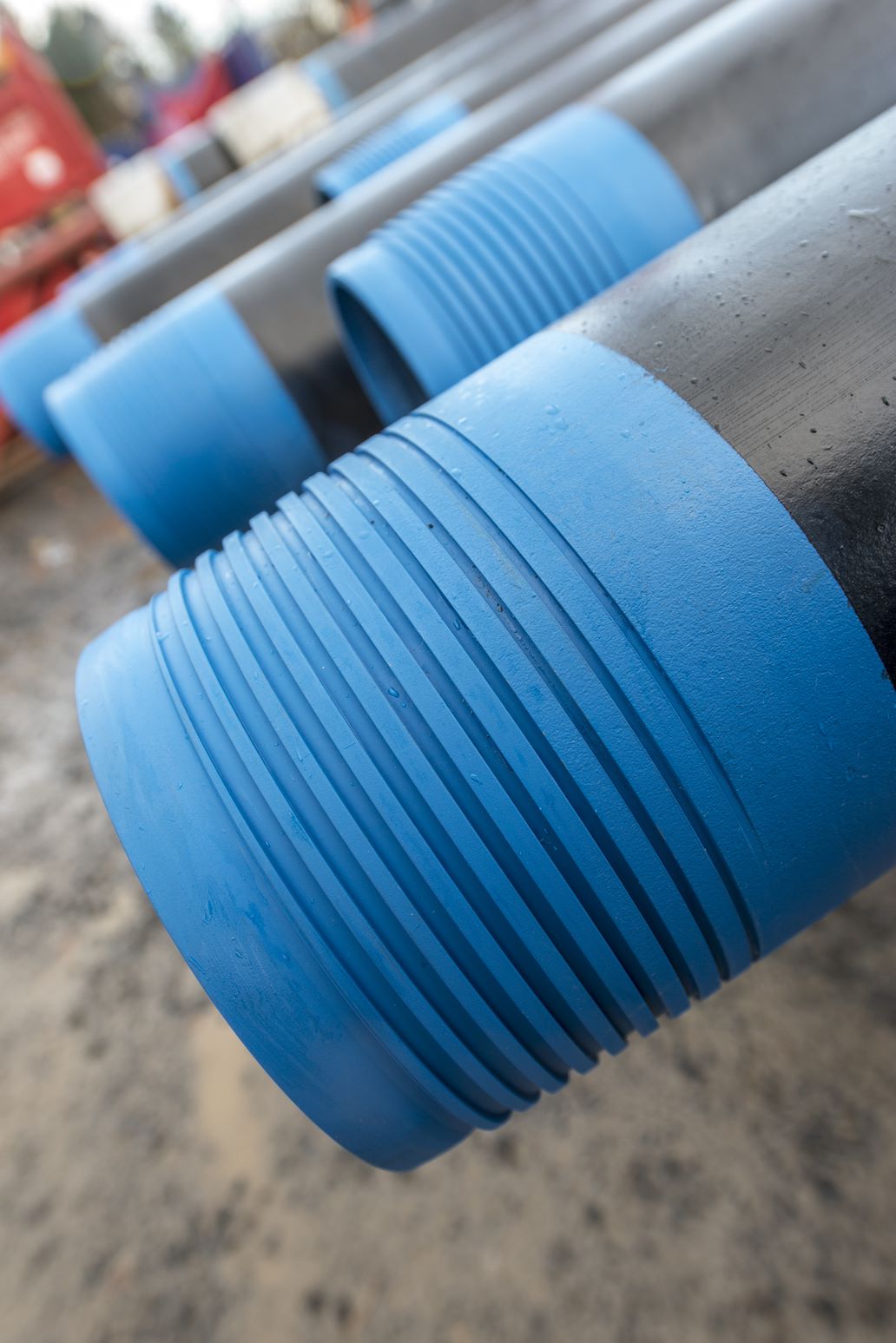
Introducing CLEANWELL® to the North Sea
In 2019, Wintershall Dea successfully introduced CLEANWELL® into their operations in the Norwegian North Sea. The first running of CLEANWELL® strings took place on an exploration project. In total, over 7,000 CLEANWELL® joints have been delivered to Wintershall Dea in Norway, for both casing and tubing, in all types of grades, from carbon steel to CRA. Most of these joints were successfully run in Wintershall Dea’s Nova and Vega fields.
In addition, local Vallourec personnel in Norway accompanied the customer during the introduction of CLEANWELL® to their operations, providing full support and availability to quickly clarify operational questions and assure the smooth transition to the new standard.
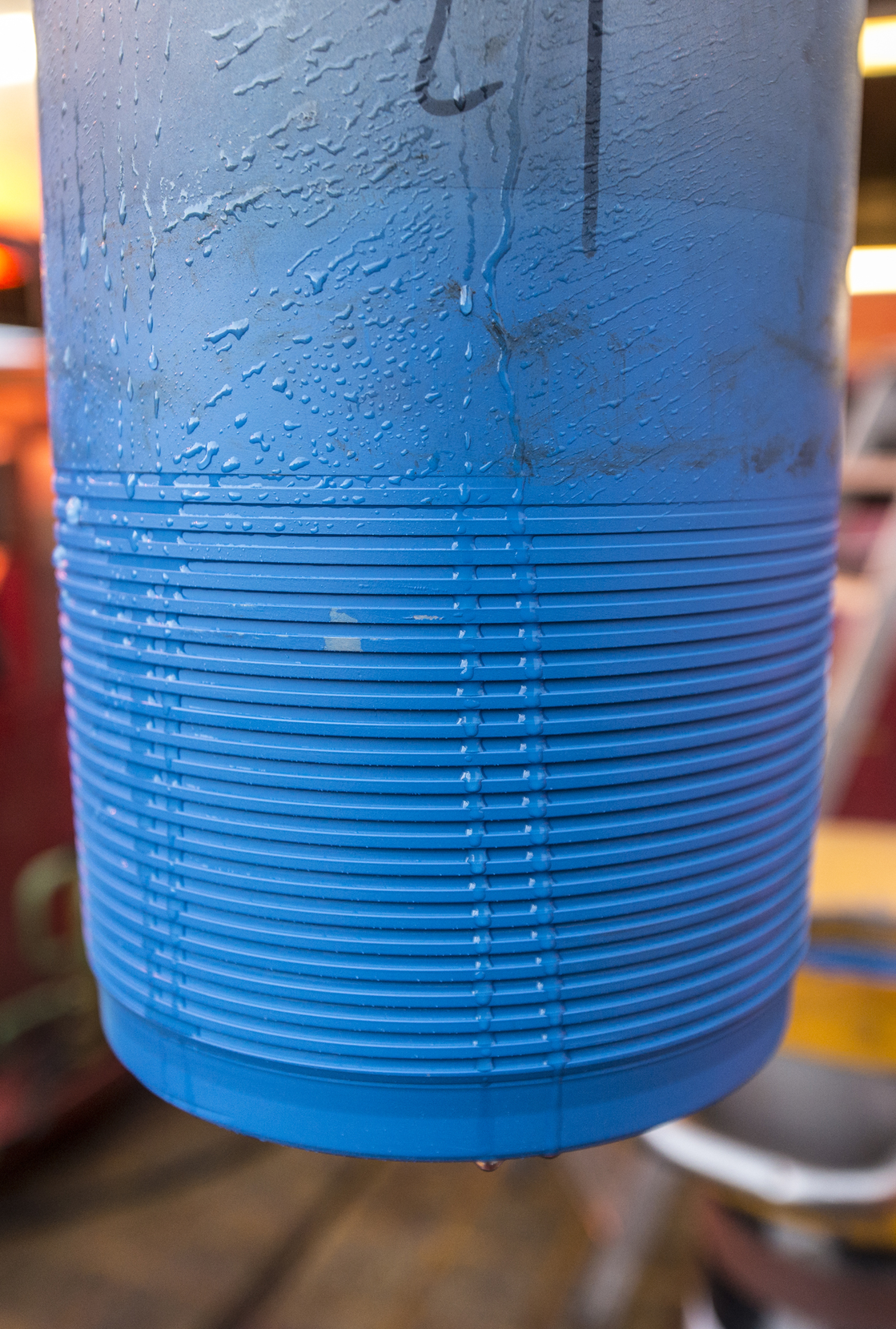
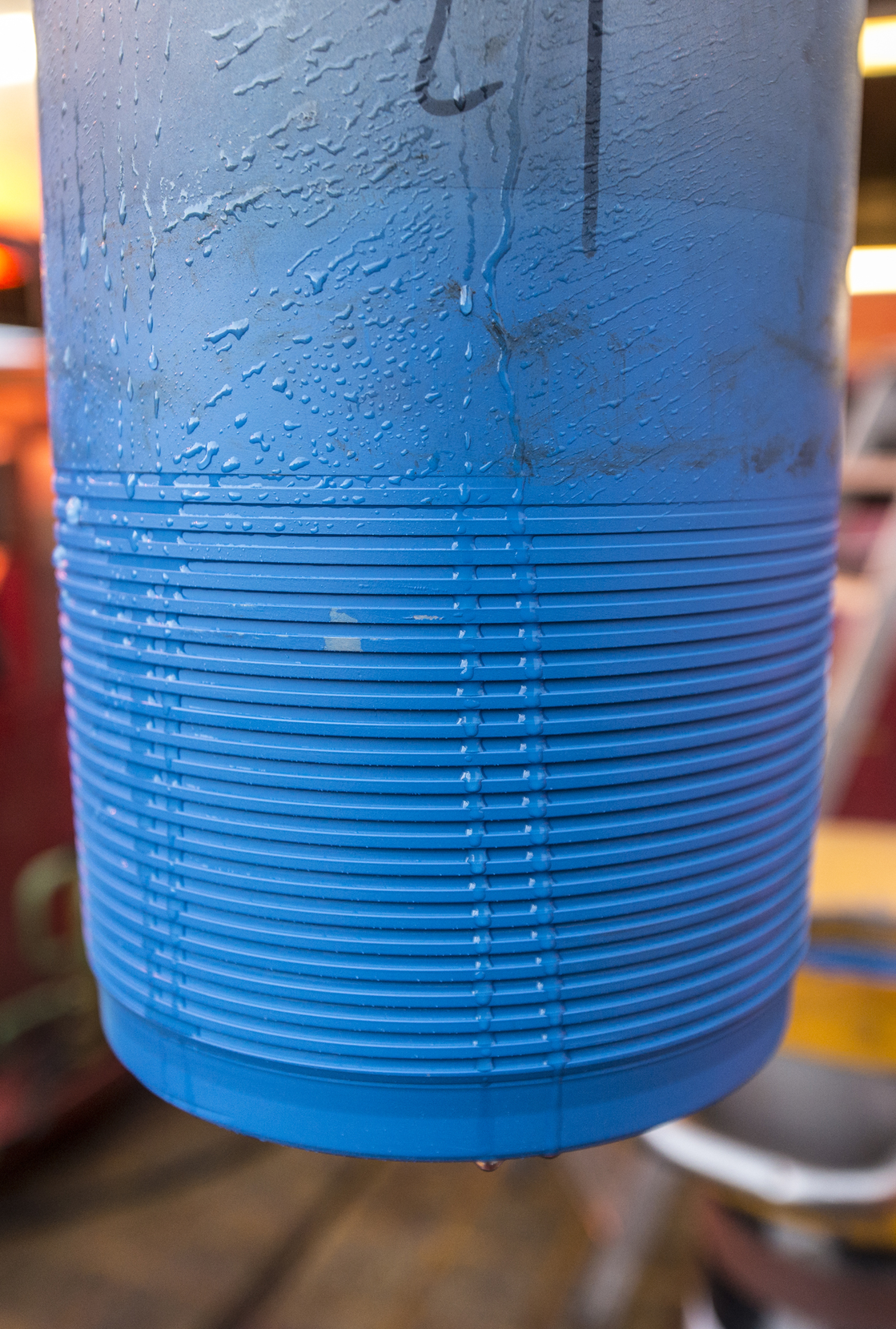
Results that speak for themselves
During the operations involving CLEANWELL® tubulars, Wintershall Dea noted a gain in efficiency throughout the pipe life cycle all while complying with HSE regulations:
- Higher reactivity upon requesting the pipe shipment to offshore rigs,
- Reduction of unplanned events during rig operations, marked by less make-up rejects, NPT and ultimately contributing to achieving running operational records in terms of joints per hour.
Wintershall Dea’s overall experience with CLEANWELL® has been positive, contributing to the operator’s decision to make CLEANWELL® a standard solution for their projects in the North Sea.