Combining operational excellence and innovation
Combining operational excellence and innovation
20/04/2021 – Innovation
A close collaboration between innovation and operational excellence is a key success factor for not only our internal performances, but also for the success of our innovations for customers.
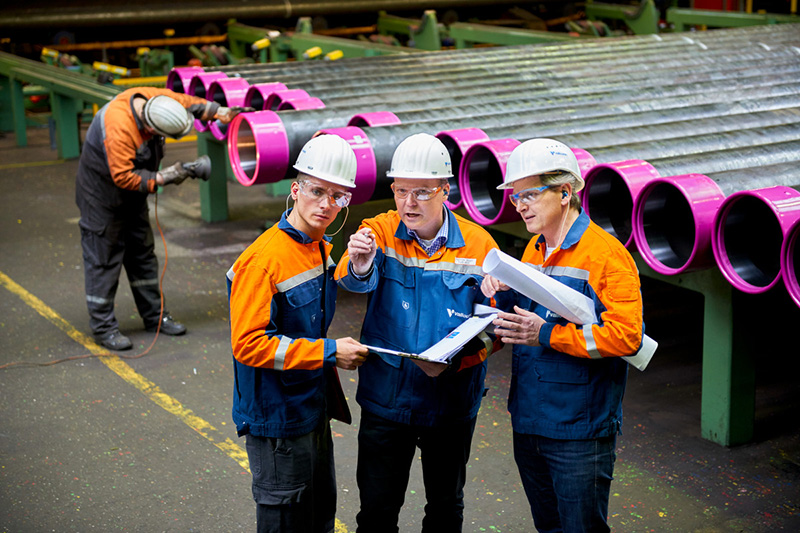
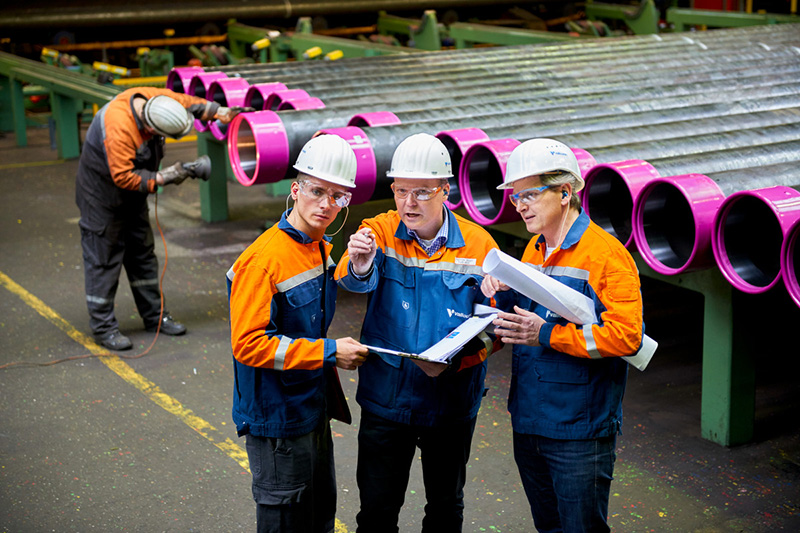
Operational excellence at Vallourec
Vallourec's Operational Excellence system aims at proposing best practices to increase the efficiency of our processes. It is used, for example, to reduce variability of stocks or lead time. This system is inspired by the principles of lean management.
They are fundamentally based on 3 principles:
- The mastering of the activities performed on the shopfloor, using simple and clear standards and indicators,
- The management routines, which must allow to quickly react to performance gaps,
- Our ability to solve problems in a systematic way, using among others the Six sigma* approach to reduce the variability of our processes.
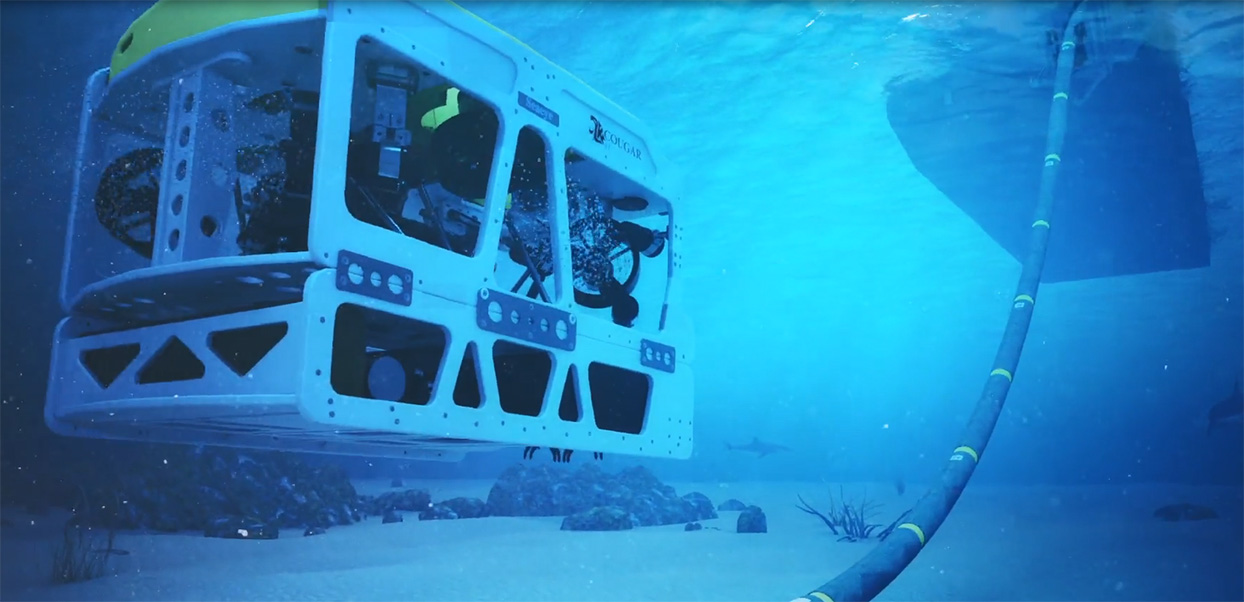
Innovation at Vallourec and innovation context in Oil & Gas
Innovation at Vallourec aims to offer to customers enhanced offers integrating new technologies.
For a few years, major energy players have also leveraged these new technologies, starting to collaborate with highly technological companies. For example, in 2018, Total and Google Cloud joined forces to develop artificial intelligence solutions applied to subsurface data analysis for oil and gas exploration and production. XTO Energy, an ExxonMobil subsidiary which is the most active operator in the Permian Basin, announced in 2019 a partnership with Microsoft. The objective is to apply cloud technology to oil and gas and improve capital efficiency. In 2019, Schlumberger, Chevron and Microsoft announced the industry’s first three-party collaboration to accelerate petrotechnical and digital solutions.
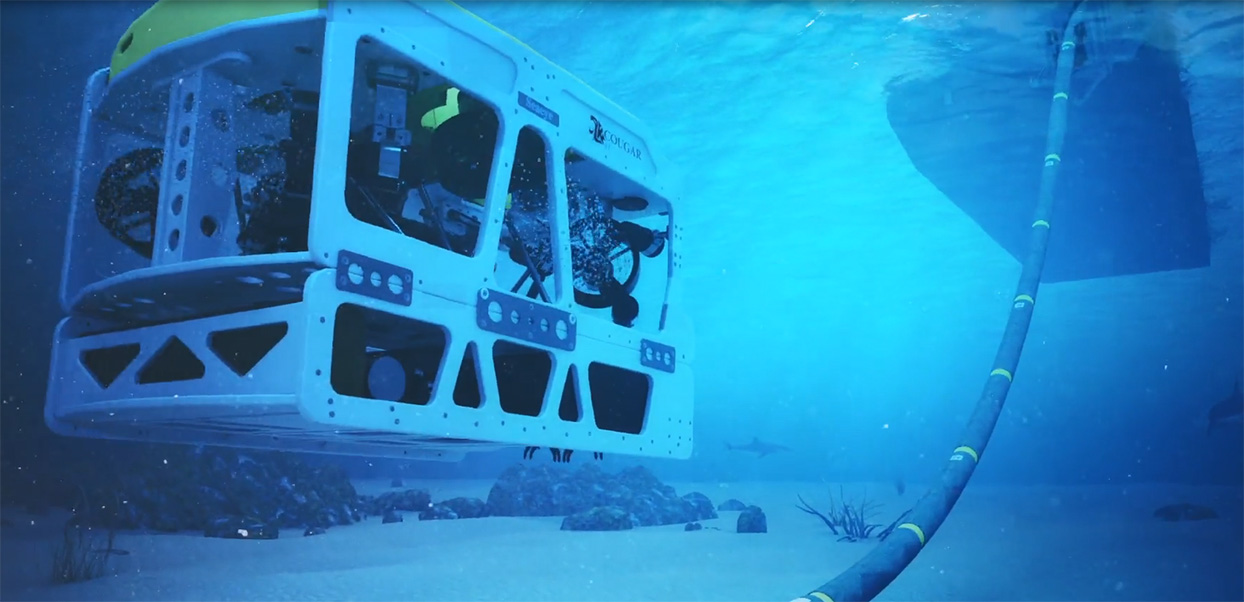
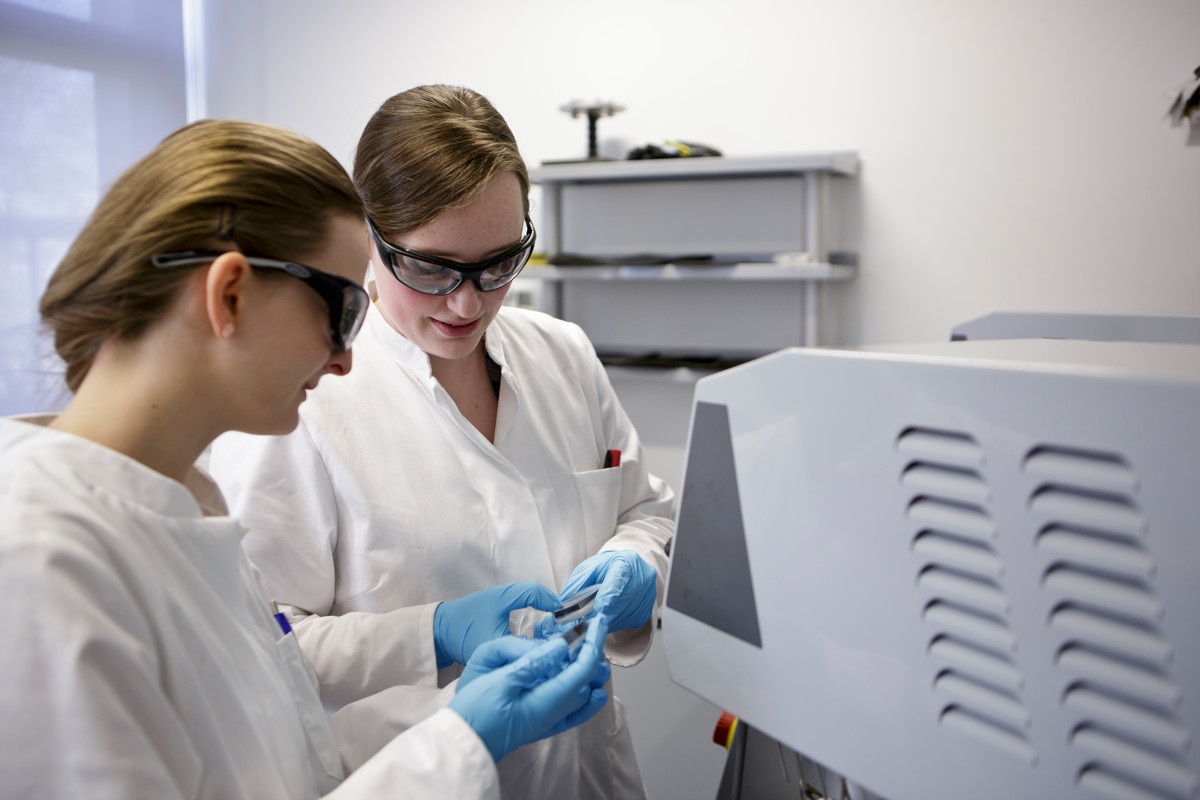
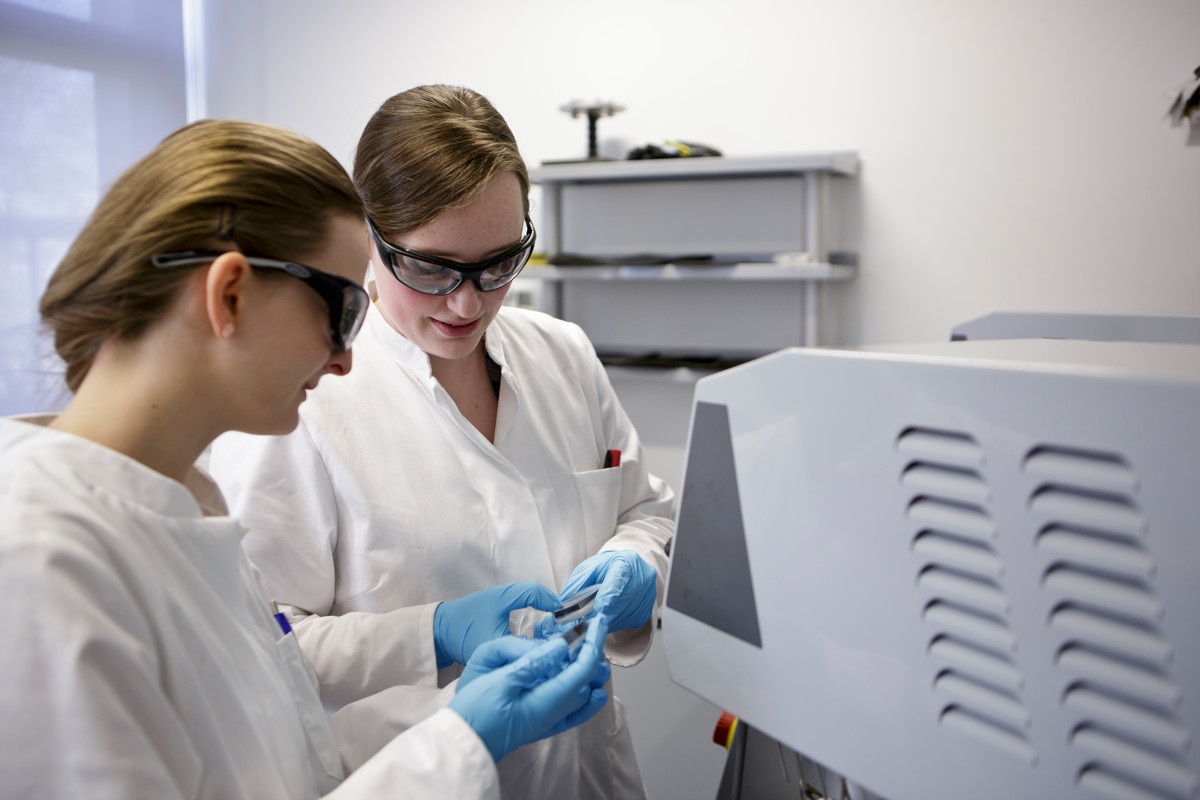
Combining innovation and operational excellence to master new technologies
It is of essence for Vallourec to fully harness the new technologies we propose to our customers through our innovations. Our own mills, with the multiple use cases we have in the mills in various regions, are great playground to develop our knowledge on the new technologies, to validate their real performances in the field as well as to identify their boundary conditions of use.
This is a reason, often underestimated, why collaboration between innovation and operational excellence is key. Of course, on top of this benefit, using these technologies for our mills is a way to increase our performances and bring internal savings.
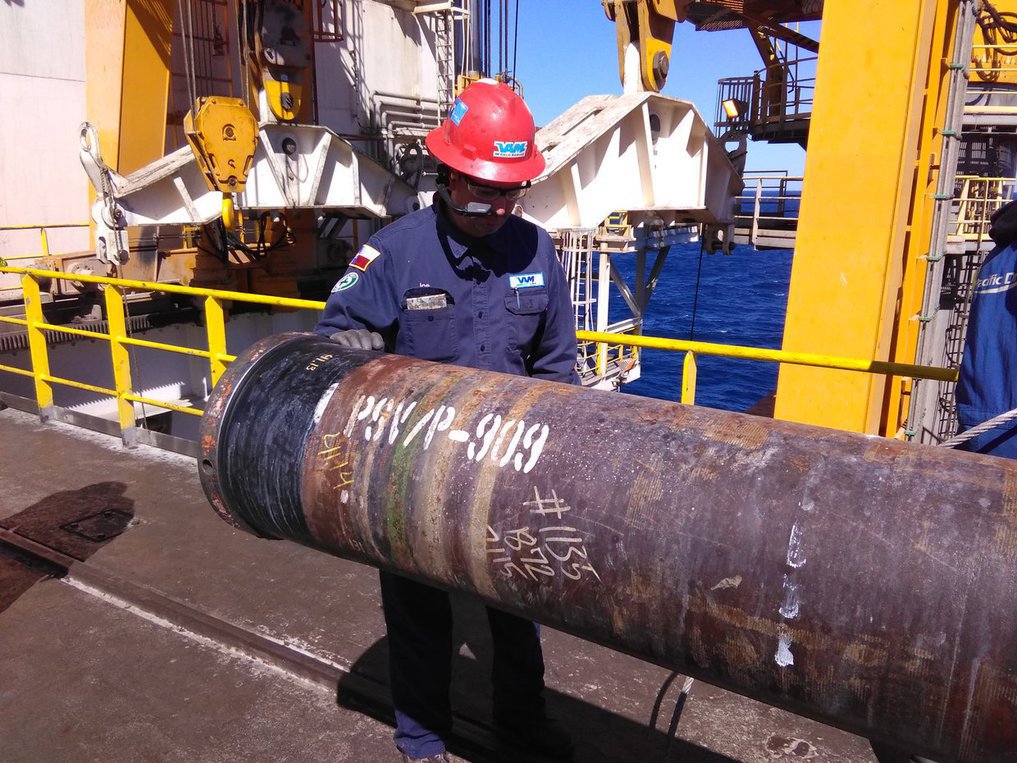
Concrete examples at Vallourec
Even before the pandemic, Vallourec began to deploy remote solutions to add value for customers. For instance, the RealWear connected headset is as simple to use as a smartphone, but keeps your hands free to do your work on the platform. Moreover, it picks up a wearer’s audio while deadening background noise, which is especially useful in an industrial environment. RealWear allows us to improve our offer, by bringing real-time, actionable information from our experts to our customers. RealWear is also of high value for internal operations, for instance to allow experts’ remote support for maintenance in mills. Having users’ feedback in the mills is key for innovation to be more relevant when discussing with customers the applications and use of our remote solutions based on RealWear.
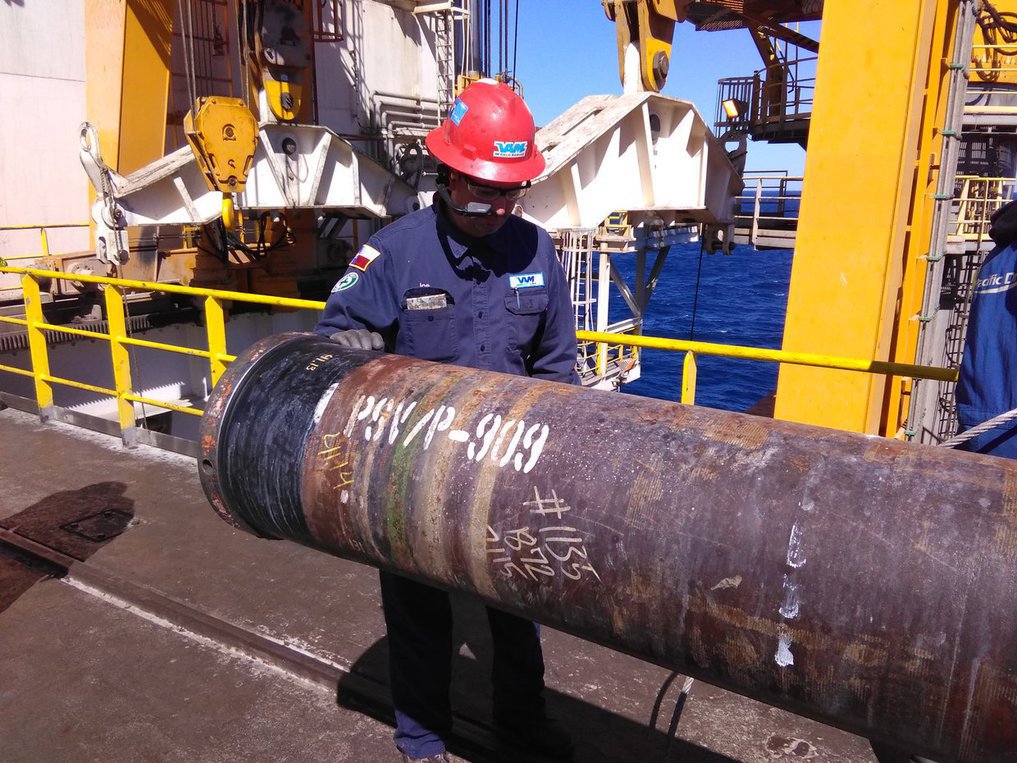
Another solution is WAAM, or Wire Arc Additive Manufacturing. It is a layer by layer deposition process of metal. This solution is a concrete answer to the very complex oil and gas value chain, which was particularly apparent during the covid-19 crisis. Additive manufacturing shortens the supply chain, allows parts to be produced with a short lead time, and reduces inventory. Using this technology in Germany for our own internal savings is a great input and increases our legacy towards the customers when we propose them cost reduction thanks to the WAAM technology.
Digital solutions to solve operational issues are numerous, namely by studying possible scenarios and proposing optimized strategies accordingly. Data applications allow us to visualize global flows, by evaluating lead time, stocks and cost price. The digital output shows the daily inventory per step, and highlights the fact that the global optimum is never the sum of local optimum.
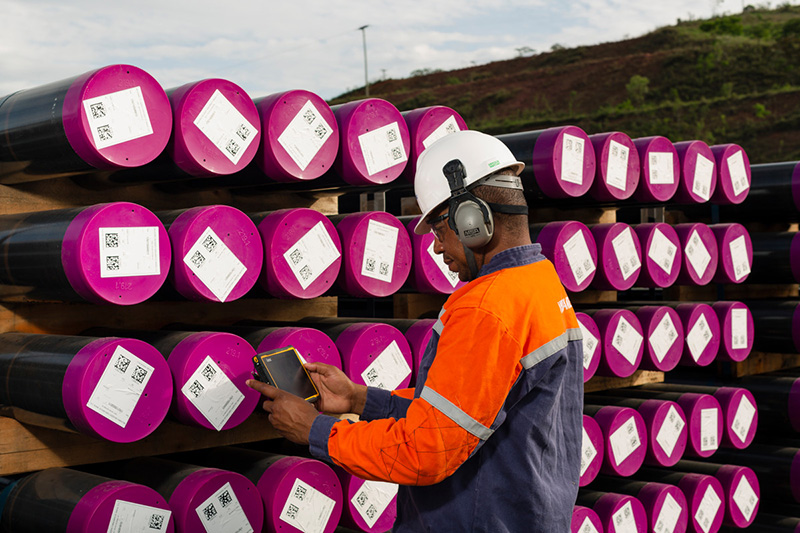
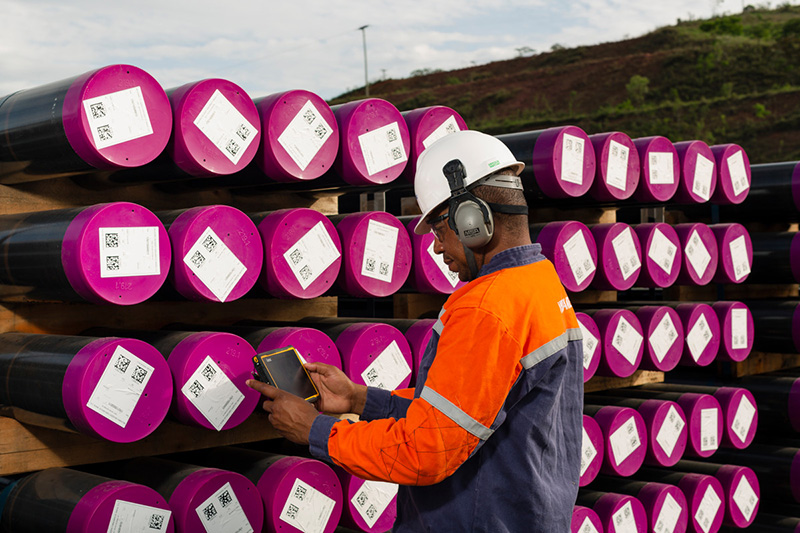
Digital solutions are already used to help our customers’ operations:
- Smartengo Inventory: a user-friendly digital solution to optimize your tubular operations by providing our customers with full visibility on their supply chain
- Smartengo Best Fit: a digital solution which provides a deterministic analysis of the data to accurately predict the HiLo resulting from all possible pipe-end combinations and anticipate operational constraints
- Smartengo Marketplace: our e-commerce platform which makes our in-stock products available to our customers in real time
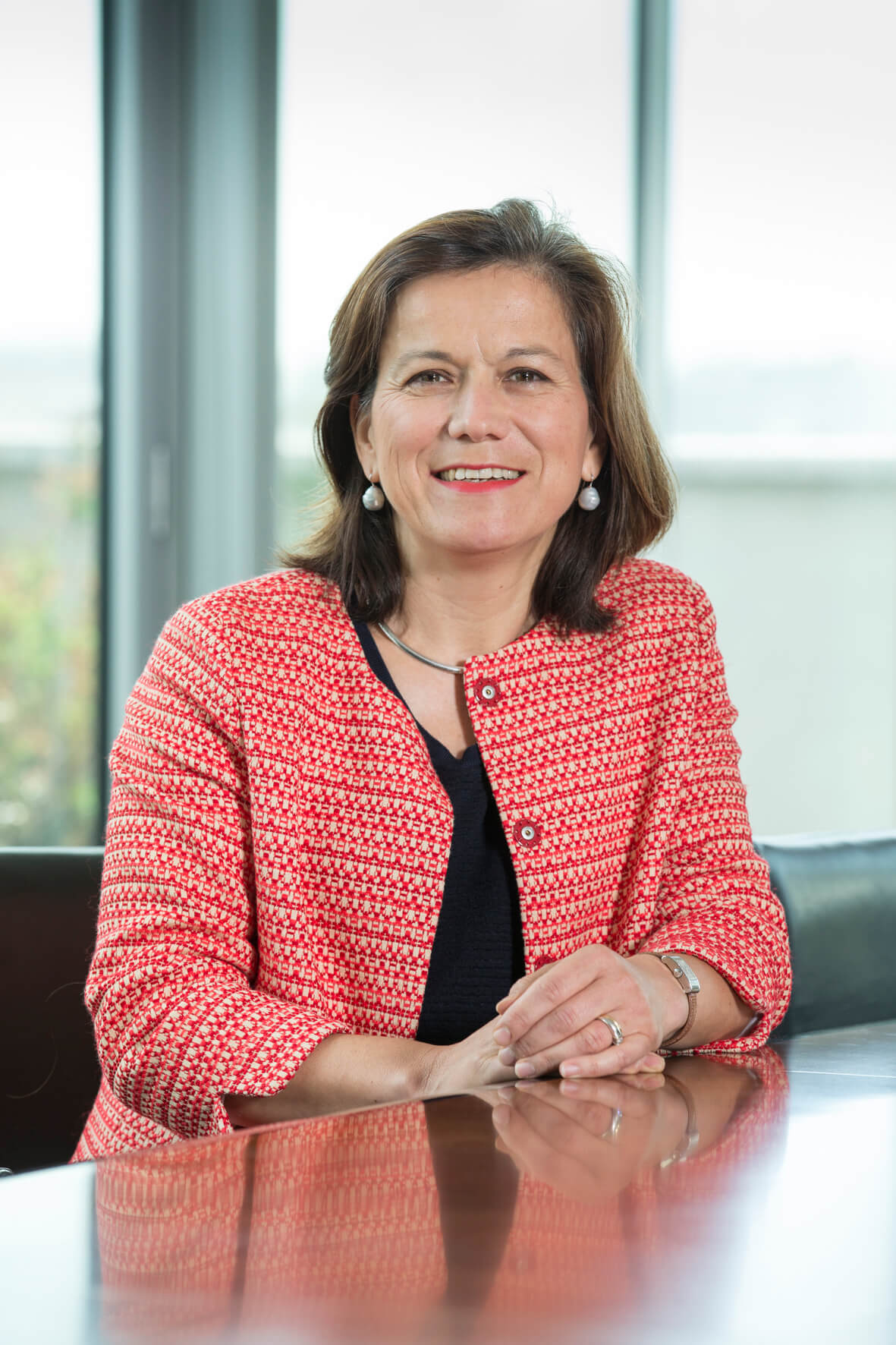
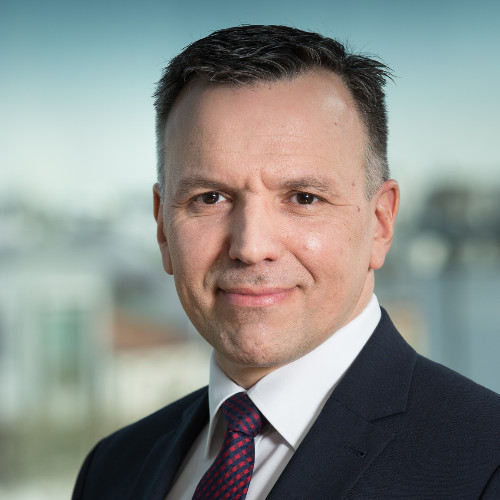