Customer & Quality Day 2022: at the core of customer satisfaction
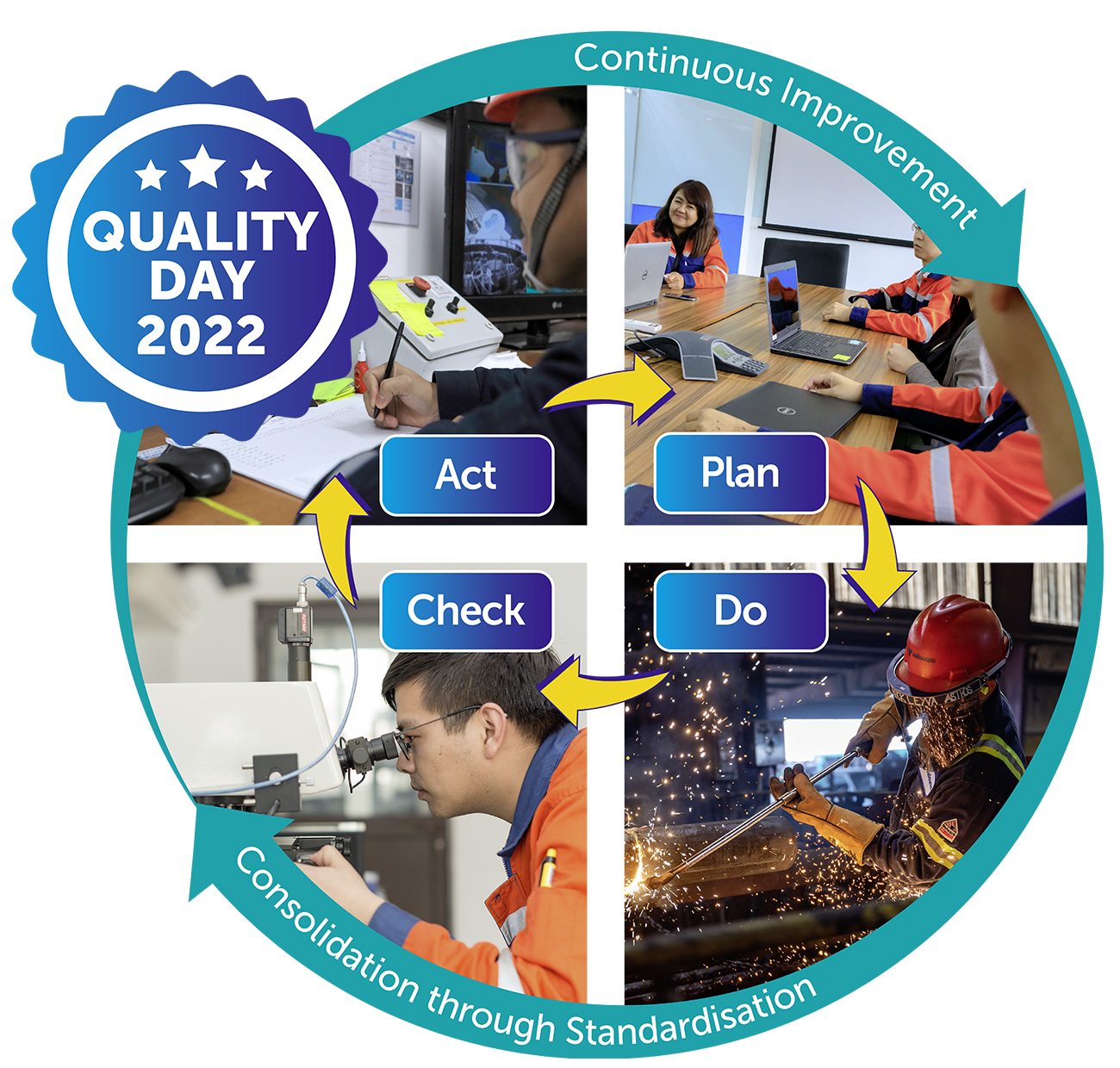
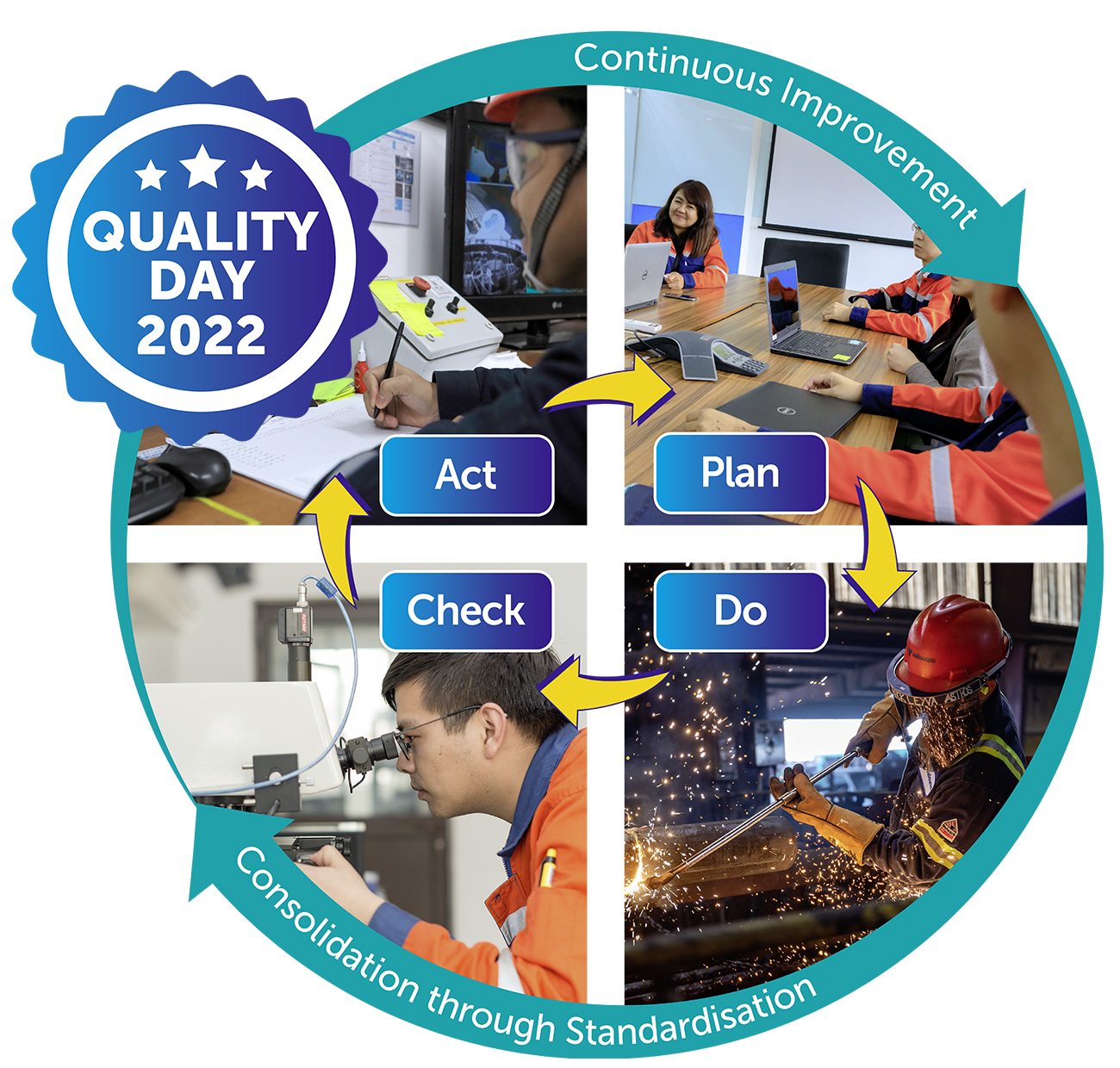
Quality is a key factor in Vallourec's relationship with its customers. All Group employees are involved in this process, which culminates in Customer & Quality Day, an event organized each year at all Vallourec sites, mills, and departments. This year, the theme of this event was the PDCA cycle (Plan-Develop-Check-Act), also known as the Deming wheel.
Already part of our quality management system and successfully implemented by several of our entities, the PDCA cycle, also known as the Deming wheel, is a major tool in any total quality approach. It allows us to easily identify the steps to follow to identify problems and solutions and thus continuously improve quality in organizations.
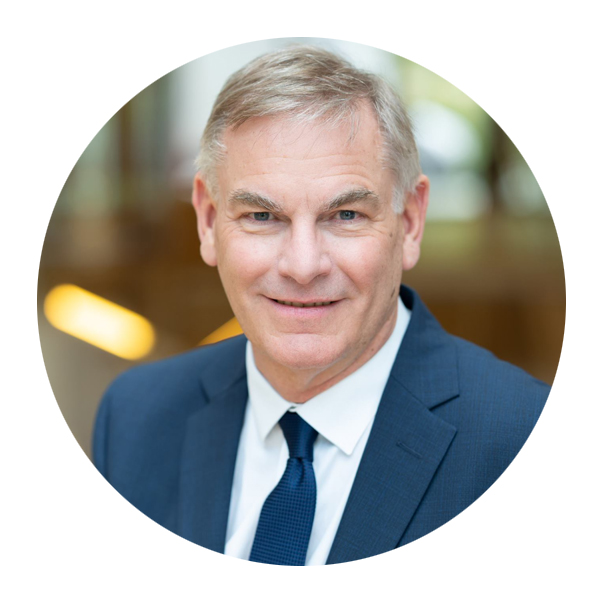
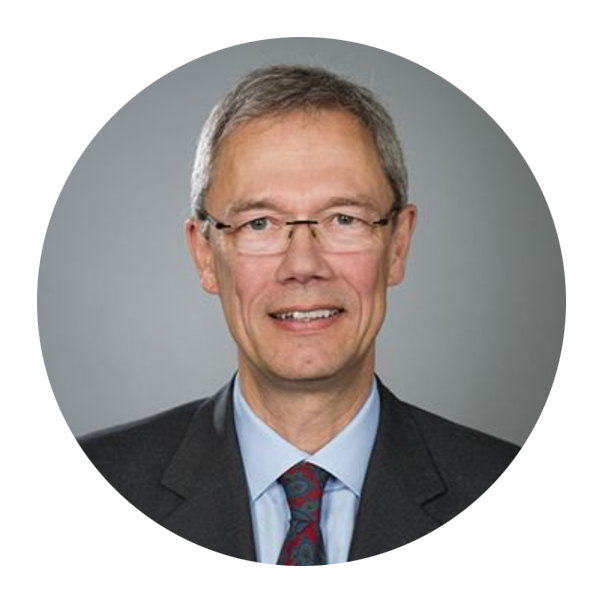
Vallourec’s mills and entities have made real progress in recent years, as shown by the decrease in the number and severity of claims and the faster responses provided to customers. But there are still some Group processes that can be improved and require constant attention, conscious action, and a regular review to identify major risks of failure and potential (if not obligation) for improvement. This is part of regular processes, both at an operational and functional level. The PDCA cycle provides guidelines for improving products and processes.
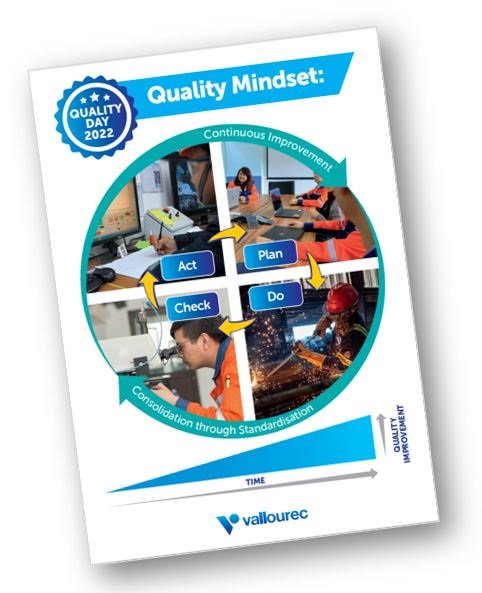
PDCA steps
- PLAN includes management leadership, a deep analysis of the current process situation and customer expectations, as well as the definition of targets and the steps to achieve them.
- DO involves onboarding people in their workplaces and rigorously executing the processes.
- CHECK involves monitoring and checking whether actions were properly implemented, and if milestones were successfully reached.
- Finally, ACT or Adapt is the remedial step, which includes the definition of standards based on lessons learned once all actions are completed.
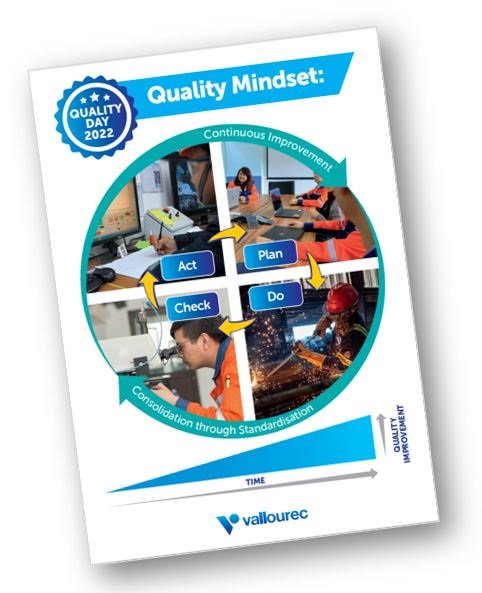
From several of Vallourec’s customers and executives, to workshops and games dedicated to quality, conferences and detailed presentations on the topic of the Deming wheel, see photos of Customer & Quality Day 2022 in the Group’s entities.