Industry 4.0: tomorrow’s industry is being built today with the Vallourec Research Center France
Physical and mathematical algorithms, digital twins, numerical modeling, big data… All of these are being deployed by VRCF’s Thermal and Simulation group on a daily basis to optimize the manufacture of our tubes and to bring about a new generation of connected and intelligent factories
Industry 4.0 is an idea and concept that appeared in Germany a few decades ago. Some still call it a “revolution” but perhaps the term “evolution” best describes these changes. Indeed, one of the basic principles of the concept is to use already existing data. For many years, our plants have been generating a lot of unexploited data. It’s like having a very complex dashboard in your car but no instructions manual.
The information is there but it is not easy to use. In companies like Vallourec, Industry 4.0 strategies have been launched to optimize the way we use this data and speed up the decision-making process. Of course, the hardware or software may need to be updated, but basically most of the information is already there.
Since the launch of the Shalyn platform, the VRCF Thermal and Simulation group has been involved in designing and producing the “software” that helps us to manage and enrich the data produced in our industrial processes.
Our role is mainly to define the physical and mathematical algorithms of these so called “digital twins”, which are digital copies of the reality of our plants.


Take for example continuous casting, which is maybe one of the most critical and dangerous processes in the steelmaking industry. It starts with molten steel from an electric or blast furnace. Via a series of cooling stages, the steel is solidified from the outside inwards to its core to produce a long steel cylinder that is then cut into “billets” a few meters long. If a defect appears during the cooling phase, it could impact the whole pipe production process, generating a pipe defect or even worse, a dangerous break in the column of hot steel.
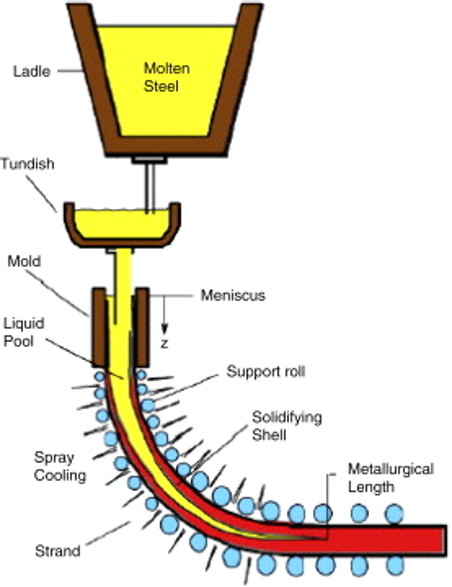
Due to its geometry and very high temperature, it is impossible to obtain an X-ray of the hot steel column in real time. We can only receive data from the surface of this column. By using a digital twin of the process, we can “see” the temperature all along the casting and also predict what happens inside it. This information helps to prevent overheating in secondary cooling zones that could lead to break out. It also helps to reduce defects that could impact the following steps of the manufacturing process.
This digital twin can also save the plant expensive trials and simplify the parameter optimization tests used to improve or industrialize new steel grades.
Therma is another “twin” designed to automatically pilot billet furnaces (the steel heating process before piercing and rolling). The last 30 years, and our increasingly fluctuating workloads, have shown that controlling the process automatically, especially billet heating, ensures more efficient gas consumption and better quality control.
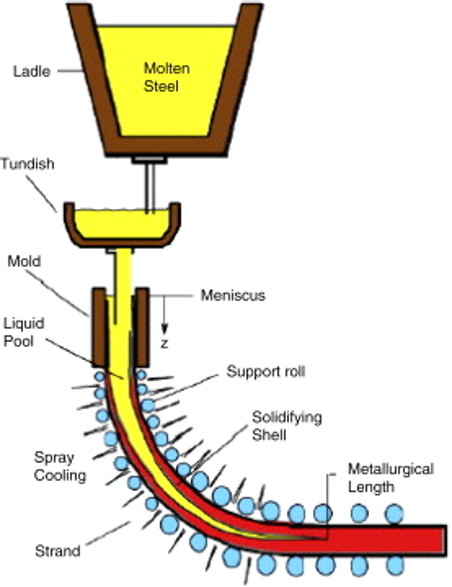
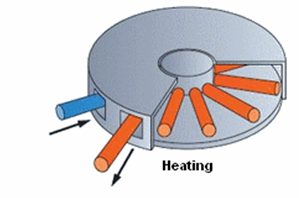
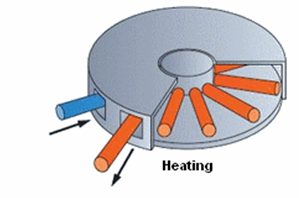
Yesterday, we expected our tools to describe the present. Today, we expect Therma to show us the future. By introducing advanced mathematical methods, more complex algorithms and high-performance computing, and by using real-time production data tracking, Therma provides forecasts of the furnace content in real-time and optimizes its operation. Consequently, Therma continuously generates large amounts of data that enable better plant management, so essential for effective production planning.
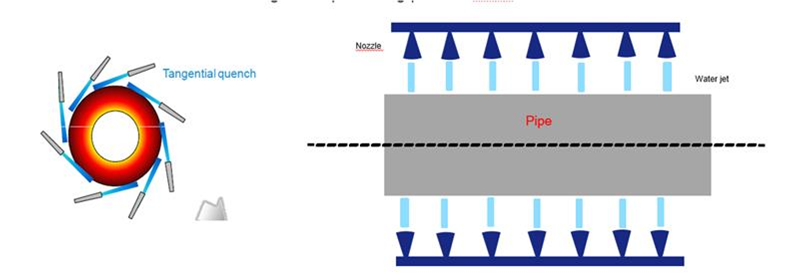
The introduction of more complex calculations requires more powerful processors and optimization of resources. To make an analogy, it is like when there was only one checkout open at the grocery store on a Saturday, you had to wait in line for ages before you could pay. Now we use techniques such as parallelization to split the different tasks involved in a calculation and perform them at the same time, as if in our grocery store several checkout lines suddenly opened at once. The ultimate aim of Therma is to generate a simulation of the temperature of each billet in the furnace (in Vallourec’s largest furnaces, there can be several hundred billets) in roughly 1 minute.
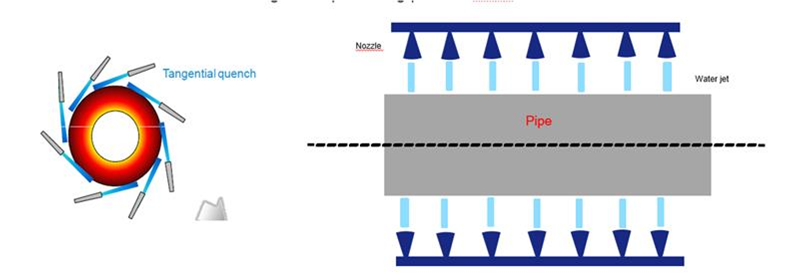
The third process concerns quenching. Key to this heat treatment process is understanding how water reacts on a hot surface, which can deeply affect the final product. You have probably already experienced the effect of water drops on a hot skillet. If you pour a little water into it, you will notice water bubbles floating on the surface which do not evaporate immediately as would be expected. This is one of the effects that we study and modelize in the quench digital twin available in Shalyn.
Today, Vallourec is seeking to increase its knowledge of quenching to test new products or improve current manufacturing methods. Indeed, knowing how the pipe cools and the final mechanical characteristics of our products offers an initial digital appraisal of pipe quality, in particular for our line pipe products or premium OCTG grades, in which the quench is the key process. For example, estimating hardness or being alerted to a risk of pipe defects, are some of the main goals of this model.
This is why the VRCF Thermal and Simulation Group has developed the Quench-R tool to monitor and generate data. This digital twin is currently installed in the Shalyn platform for simulation purposes and is shortly to be deployed on the Rath 16” heat treatment line.
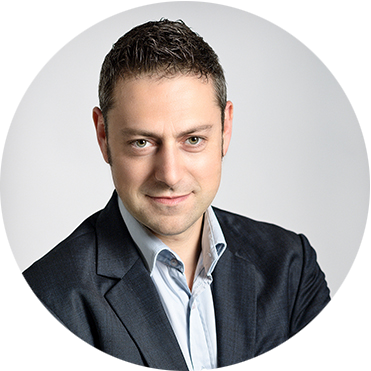
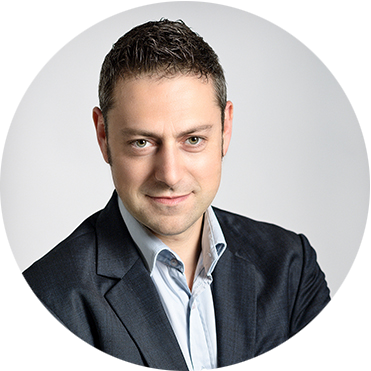
Marcello Bentivegni
Manager Pole Thermique et Simulation des Procédés
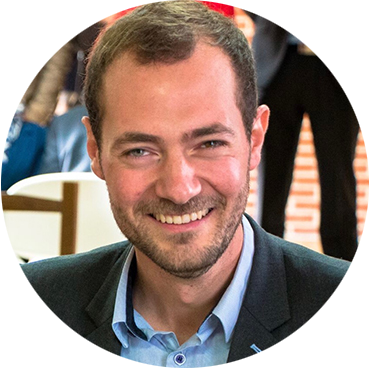
Guy Druart
Manager Equipe Modélisation
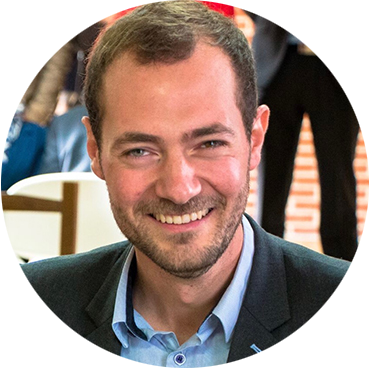
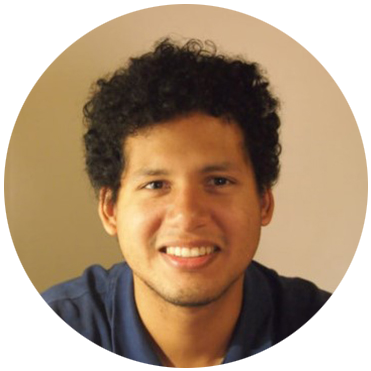
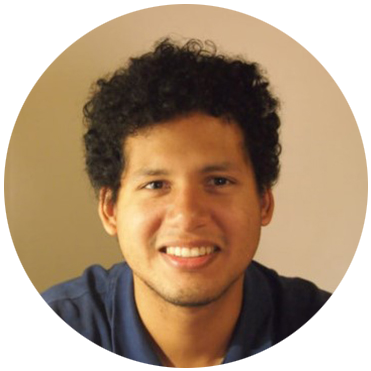
Juan Huapaya Otoya
Ingénieur R&D
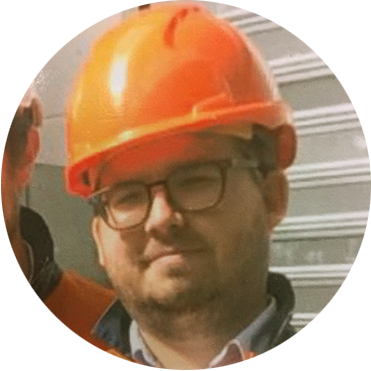
Thomas Lenne
Ingénieur R&D
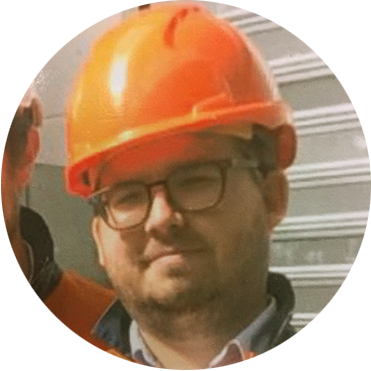