Vallourec excellence in 4.0 mode
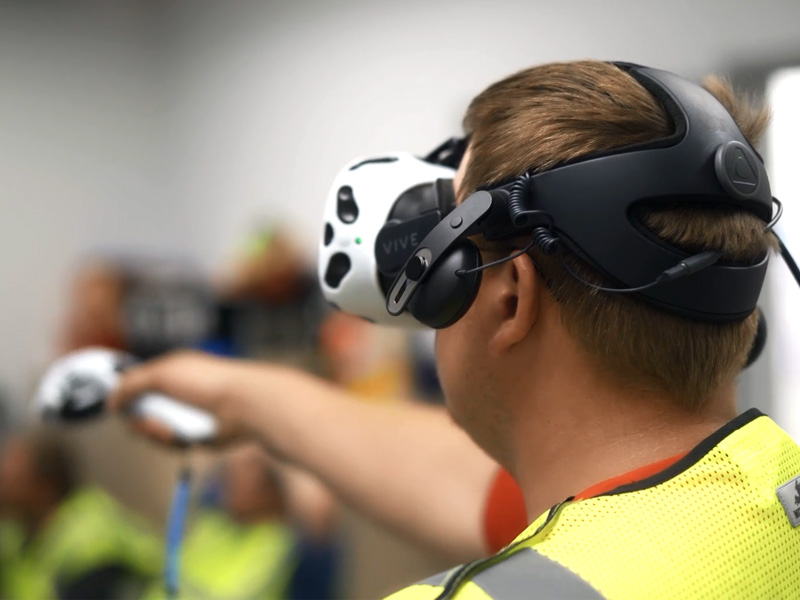
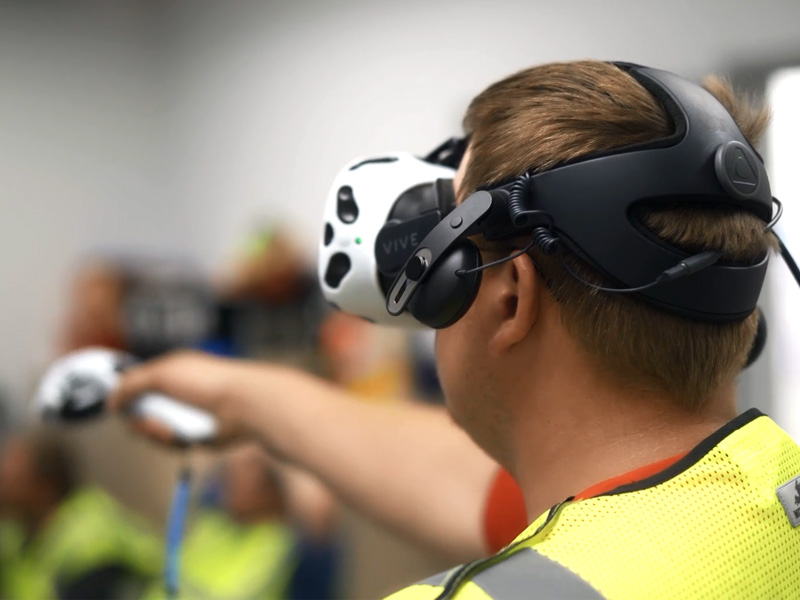
Moving into industry 4.0 isn’t about replacing existing factories with brand new facilities, but about instigating a transformation. It involves placing technological bricks one by one, until laid end to end they pave the way for a revolution...
A fourth industrial revolution
The term “industry 4.0” was first used in 2011 at the World Industry Forum in Hanover to describe a new way of manufacturing in a new generation of connected factories.
Why now? A number of technologies are reaching maturity: data, augmented reality, the industrial internet of objects, advanced robotics and the cloud. They all come together in 4.0, which sets all players in the value chain on the path to a true revolution.
Coal power and the steam engine marked the first industrial revolution and superseded handcrafting. At the close of the 19th century, the use of oil and electricity brought about the second industrial revolution and ushered in mass production. The advent of electronics and computing brought robots to assembly lines and heralded the third industrial revolution. The age of customized products and small batches is the latest challenge facing industry, which is launching its fourth revolution by means of data and connections.
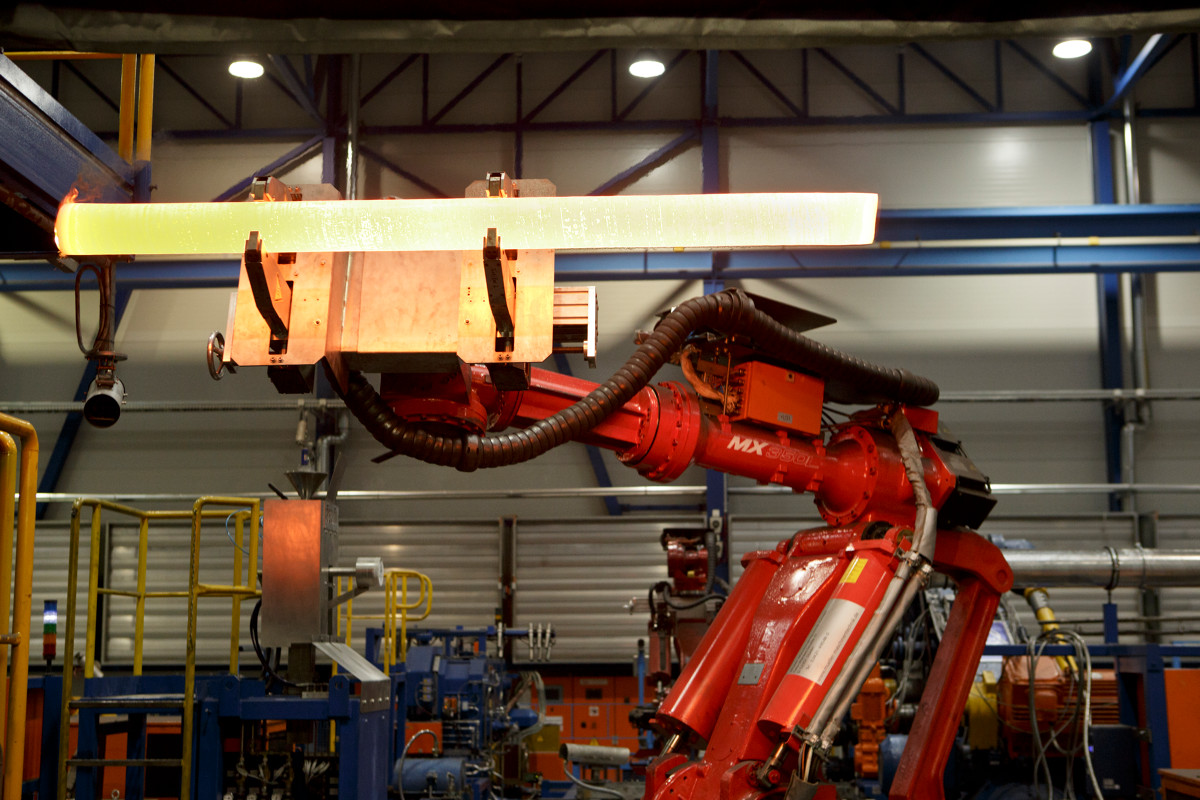
Digital transformation involves the whole of Vallourec in a four-dimensional strategy:
To connect customers with factories and with products, make life simpler for employees, and shift into industry 4.0 with determination, but in a controlled way. “Industry 4.0 is a boom area where everything moves extremely quickly,” explains Marc Brémont, Vallourec’s industrial Master Plan Director responsible for the digital transformation of its factories. “For greater efficiency, we decided to concentrate initially on three areas: big data and simulation, augmented employees and additive manufacturing, to which we have recently added advanced robotics.”
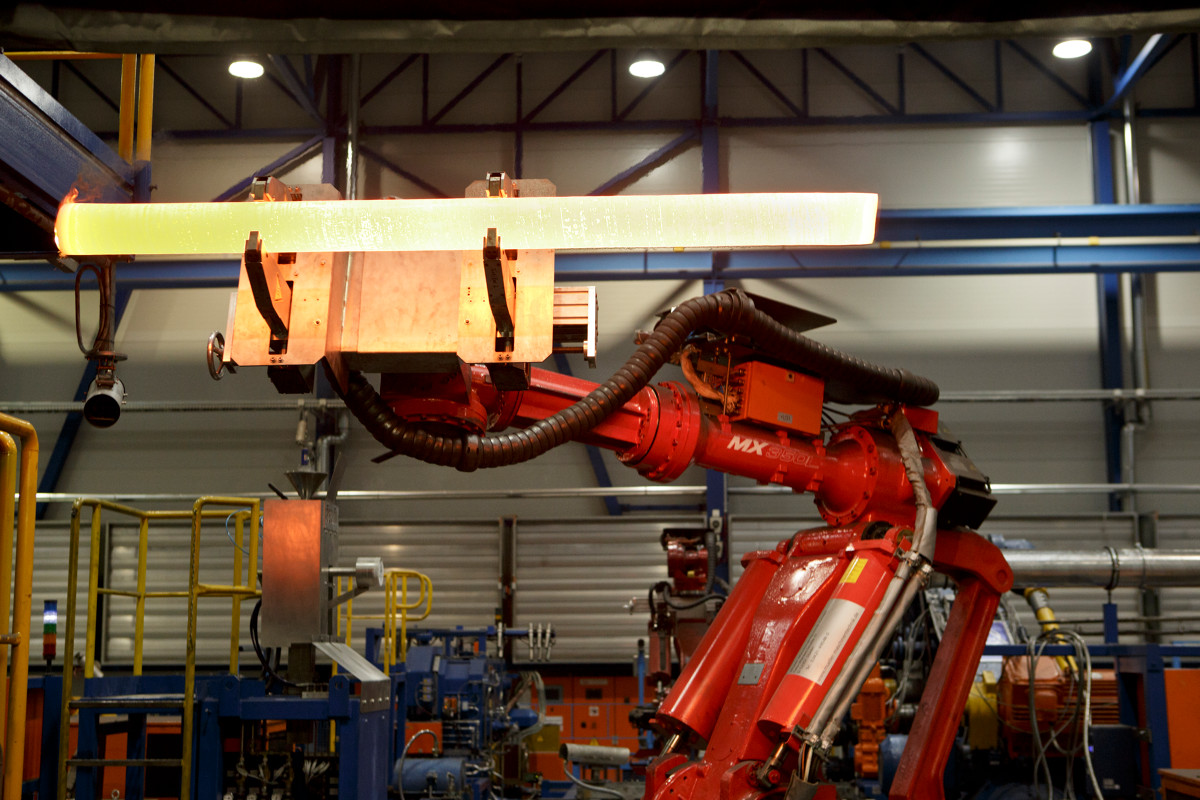
Experiments around the world
In terms of 4.0 technologies, Vallourec is ahead of the curve.
In the first area, data science is revolutionizing manufacturing processes around the world, multiplying simulations with the help of machine learning models and advanced algorithms. Vallourec Star (USA) optimizes the energy consumption of its electric furnace in Youngstown and can predict thread defects from the moment the tube exits thermal processing, while the Rath rolling mill in Germany can predict tube thickness and correct the slightest discrepancy in real time. For its part, Vallourec Brazil is increasing productivity by fine-tuning its production sequencing.
In Déville-lès-Rouen, the 4.0 journey is human and makes life easier for maintenance operatives and production managers by “augmenting” them with real-time performance monitoring tools. A suite of digital tools enables them to detect early signs of breakdowns and make plans to repair them without interrupting operations. It now takes just seven hours for a tube to travel the entire production line (compared with one or two weeks before the machines were networked) under the watchful eyes of the staff, who monitor flows in real time and optimize them if required. Touch screens have revitalized meetings with short, standardized formats (Theme, Objective, Plan) for greater efficiency, and no one would want to turn back the clock.
Focus on thrilling technologies
Better known as 3D printing, additive manufacturing cannot yet make tubes, but already makes it possible to produce parts to the required dimensions from a raw material (powder, wire or metal) in a very short time frame. Bertrand Maillon, head of the additive manufacturing project at Vallourec, sees it as an opportunity to “take the customization of our products to the next level and assign a specific function to each tube according to its position in the pipe system.” Additive manufacturing has already brought about the first accessories order, prototypes, an OCTG tube augmented with a centering function, and quick drafts. An internal incubator involves customers in defining and experimenting with the value offers they want. Customers then benefit from custom solutions that can be reproduced rapidly on demand, enabling them to reduce warehousing costs and avoid supply shortages.
For its part, advanced robotics is indispensable for eliminating tedious or dangerous tasks. The robots are now equipped with artificial sight that enables their use in complex configurations, with a level of precision that is often difficult for a human operator to maintain over time. In Rath, Germany, robots on the production line precisely measure the geometry of the tubes, while in the United States, robots perform traceability operations on the tubes directly they exit the mill, something that could not be done manually.
Benefits of 4.0 for everyone
“We’ve already identified savings of many tens of millions of euros over the next three to five years,” says Marc Brémont.
“Mainly because this will enable a major qualitative leap in how we control our manufacturing procedures.” For customers, industry 4.0 promises customized and enhanced products, and cost savings too. For employees, their agile tools and methods encourage collaboration and an overall increase in skills. The operator takes control, while the manager coaches him and the engineer can devote herself to innovation. Lastly, for the Group, 4.0 is a lever for industrial excellence and new competitiveness to ensure Vallourec’s sustainable growth.